A Week in the Shop
Published 22 Apr 2023
Tags: fretwork, necks, paintstik, plectrums
It’s been an interesting moment, one that I feel should have been more of a cause for celebration, but one which I approached with a little trepidation: the Älgen guitar, the part 3D-printed one, came home with me so I can live with it as an instrument for a bit:
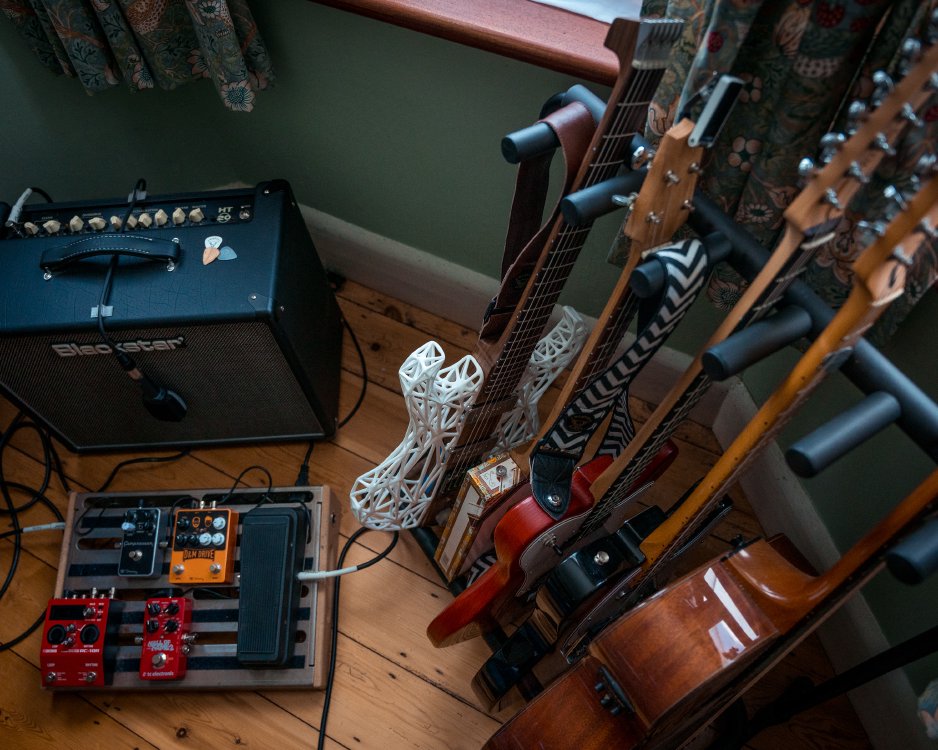
I never imagined when I first designed Älgen back in 2021 how long this build would take, nor all the bumps that I’d hit along the way. Älgen’s been such a feature of the workshop build process this last two years that it’ll take a bit of time to relate to it as an instrument rather than a technical challenge. But it is truly lovely to get to finally play what is a unique instrument and make music with it. It’s weird seeing it in my guitar rack with the other instruments, but it’s nice how it stands out as something unique, but not too much: it’s still obviously recognisable as the instrument it is.
The end isn’t there for this build quite yet: part of playing it now is to work out what needs tweaking, what works and doesn’t with this new design that I’ll want to improve on for the next iteration. I imagine I’ll write up some of this in the coming weeks, but for now I’m just letting myself enjoy playing it as much as I can, using it as my daily driver to force me to engage with it properly as a player.
On a related note, as I’ve mentioned before, the name “Älgen” is Swedish for “The Moose” and the name relates in part to having watched “Den Stora Älgvanderingen”, or “The Great Moose Migration”, which Swedish public broadcast television, SVT, streams each year to watch the moose as they migrate north past a particular river spot. As I write this SVT went live for this year’s broadcast. It’s a very relaxing stream, which I look forward to have on in the background for the next couple of weeks, and each year you see about fifty meese swim the river. If you want something calming in your life with occasional “will they/won’t they swim” moments of excitement, then I can recommend it.
The timing of finishing Älgen is coincidental, but feels very appropriate.
Älgen
Before I brought Älgen home, I still had to finish off the last few bits hanging over from a couple of weeks ago. Back then I was having issues with the D-string snapping repeatedly, and my workshop-mate Jamie had suggested that I should try de-burring the bridge tuners, as he finds rough edges on tuners a common cause of breakages in the style I was having - just the edges on the tuners are left sharp from machining and causing the strings to wear out where they touch that.
When last in the workshop I had used an old wound string to try de-burring the tuner, flossing it essentially. At the time though I was out of spare D-strings, and had to wait for my order of a bunch more to arrive (thank goodness you can buy individual strings!). I ordered half-a-dozen, just in case I still hand’t got to the root cause, but obviously having done that the first one went on without any issue and has stayed there fine since. So fingers crossed that’s the end of that particular saga. Only time will tell I guess, but next time I change the strings I’ll repeat the de-burring process on all the other tuners just as a precaution.
I finally got to try the Markal Paintstik+ that Brad Avenson recommended to me which I also mentioned a few weeks ago. I was a bit puzzled as to how they work, as the Markal site doesn’t really have instructions on them, but in the end you just use them like a crayon, but you have to wear through the outer layer of the stick that has dried a little (I’ve seen some videos on YouTube where they also will use a knife to remove that outer layer before use). I tried it both on a laser-etched bit of acrylic that is on the back of Älgen, and on the 3D-printed volume control:
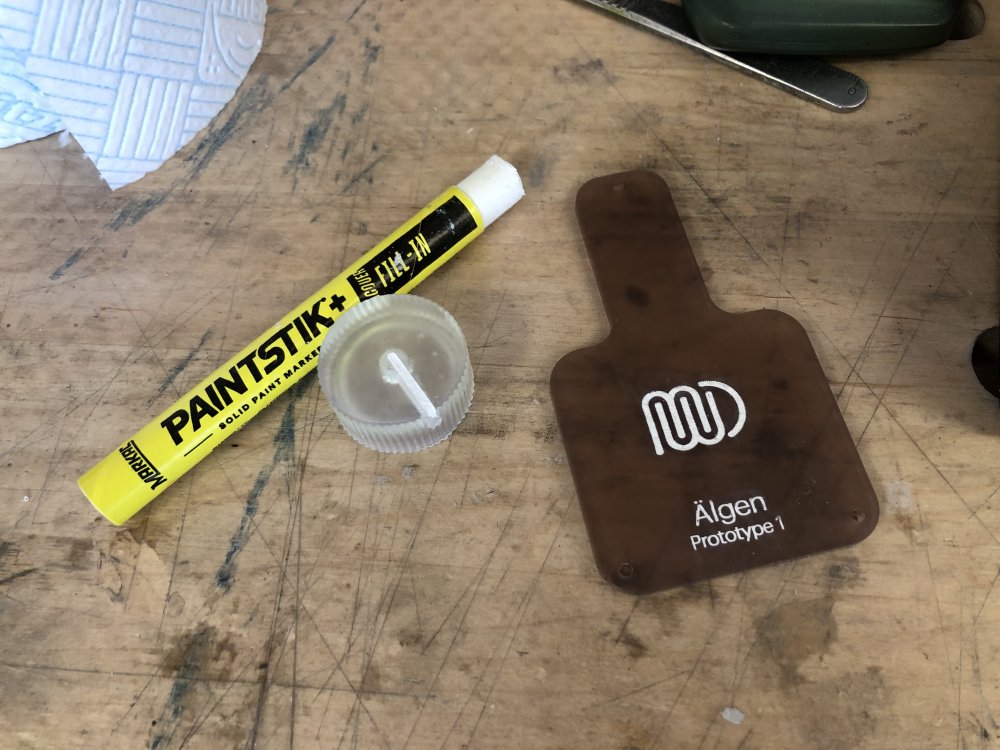
I think the trick is that in both cases I could have done with a more shallow recess to fill. I had to use quite a lot of “paint” to fill the recesses on both parts, and as a result the finish is a bit lumpy. The other trick, which Brad passed on, is that you’ll end up with some on the top surface around where you’re trying to fill, but you can wipe off the excess using white-spirit or other similar mineral oil.
Still, I was happy enough with the result that I was able to install the last part on Älgen:
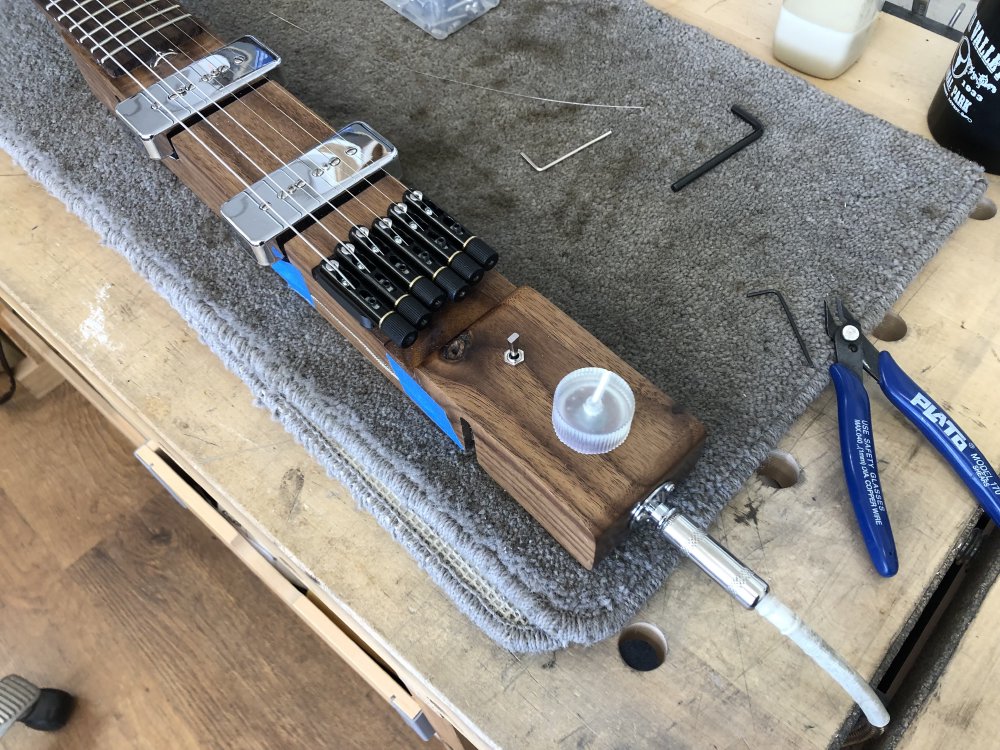
This is the forth iteration of the design for the volume control, which is the joy and curse of 3D-printing: you get to make something bespoke, but given you’re making a part that hasn’t existed before it takes a few tries to get it just right. In this case it took me a few goes to get the internal recesses just right for it to grip the pot properly and sit flush with the body.
Verkstaden
In last week’s notes I was focussed on doing the fret-work on the neck for the Verkstaden build, having left it about 1/3rd through the way of dressing the fret-ends. So that’s where I picked it back up this week:
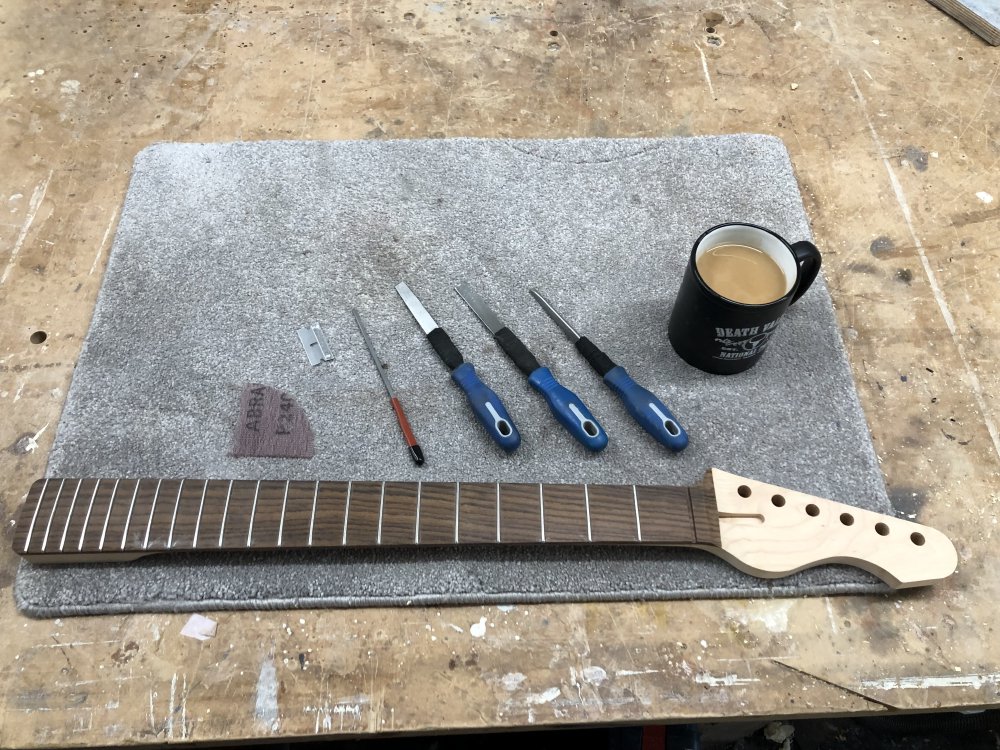
Then I got to spend some quality time continuing to work on my fret-end rounding skills:
It’s still quite a slow process for me, but I’m getting there with my technique. In the past, out of fear of damaging the fretboard finish, I’d obsessively masking-tape up the fretboard leaving only the frets showing, as see here in this picture from 2018:
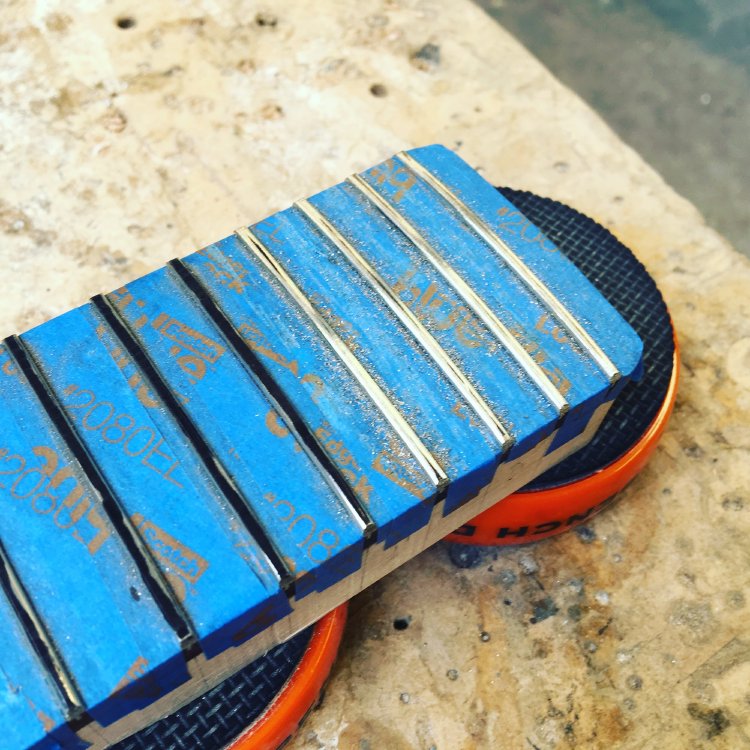
But now I follow my workshop-mates lead in not doing that, just operating on the neck without any safety layer. Taping up the neck like that is a lot of effort, and doesn’t always save you: any mark that might actually damage the fretboard proper will probably tear through the masking tape anyway, at least in my experience. It does save you from sharpie ink getting into your fretboard, but that’s easy enough to clear off using something like Liquid Gold. It’s a bit scary at first, as you will mark the fretboard a little when filling as the tools run against the wood, but by the time you’ve sanded the frets you’ll rub that out and you’ll never know.
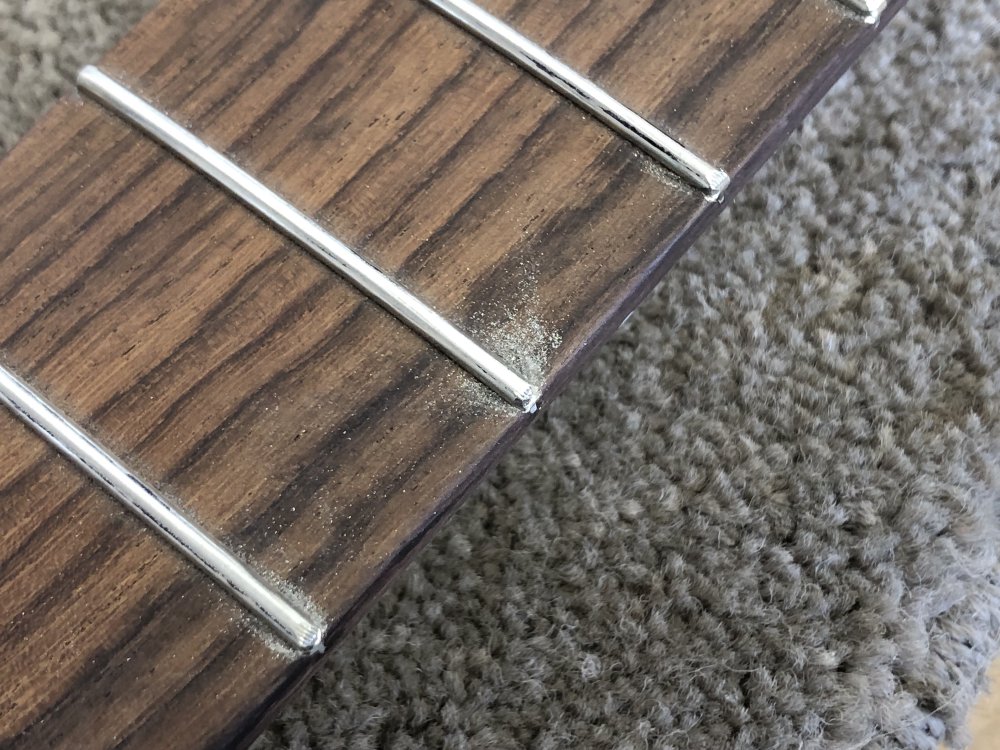
I suspect it took me another hour to get all the fret ends done, and by the end, whilst again it looks not quite a perfect as my workshop-mates, in the important test of how does it feel when you run your hand along the fretboard, I’m really pleased with the results. One of my aims for my “phase two” as a builder was to get better at the necks, and in particular the frets, and I can definitely see and feel the results.
I did want to print a bridge for Verkstaden this week, but alas the Markforged printer I’ve been using at the local maker-space was out of action.
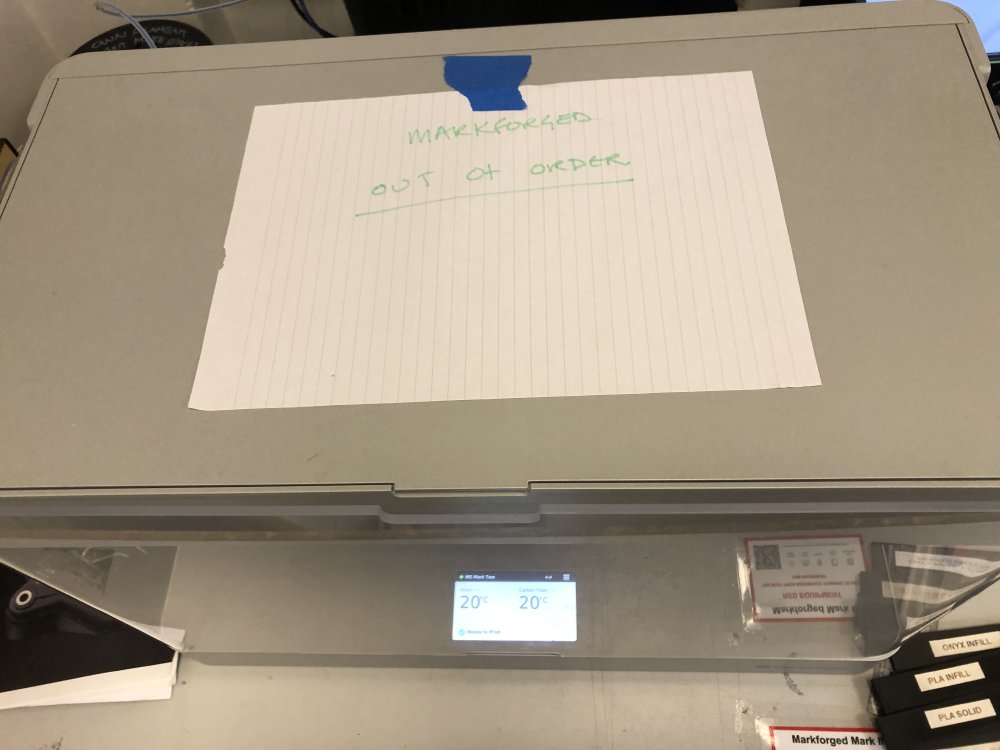
Thankfully this isn’t an urgent thing, so hopefully it’ll be fixed shortly and I can get that printed.
Delfin
All the work on the neck for Verkstaden means I now have two necks at roughly the same stage, the other one being for Delfin.
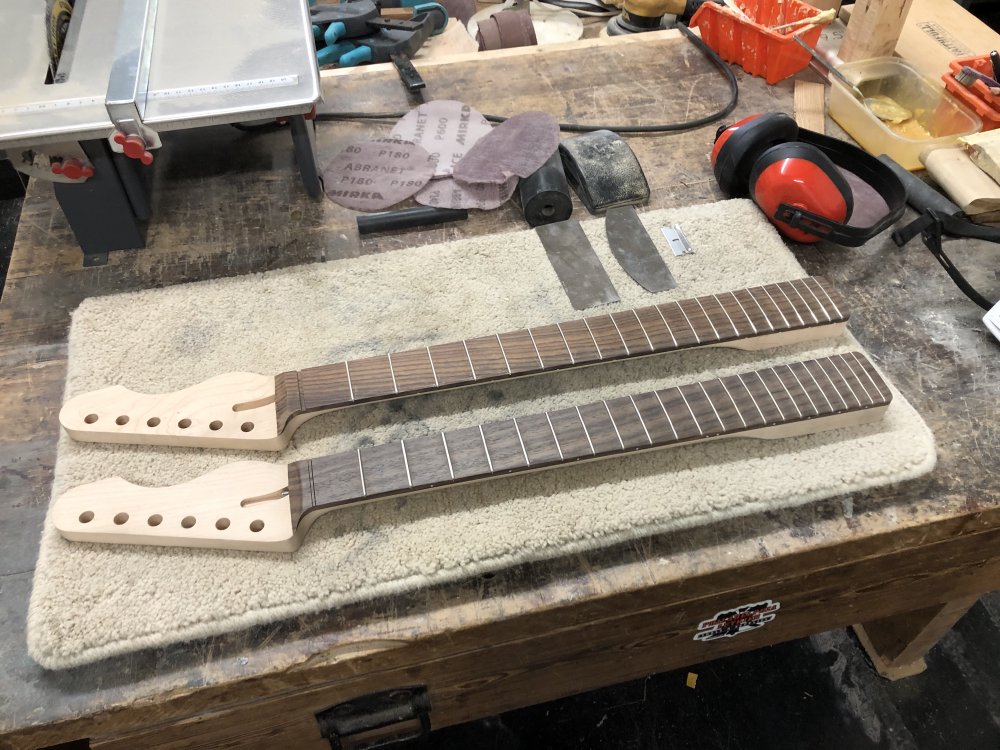
Other than the colour of the rosewood being slightly different, the two necks look quite similar in the photo, but in practice the neck for Delfin is notably shorter in person, as it’s a 24" scale-length versus Verkstaden’s 25.5" scale-length, though oddly Delfin has one more fret despite being shorter. This is the kind of anomaly that falls out of the fact that my short scale-length and long scale-length guitar designs started from different places, even though they share a bunch of design queues. It is definitely something I should try and unify at some point.
Anyway, the only job left on Delfin’s neck was to cut the nut slot. I’d marked out either side of the slot when I cut the fret-slots, and so I used a small angled chisel to remove the material between those slots. The angled chisel is quite nice for this, as it means I can follow one edge or the other without cutting beyond it.
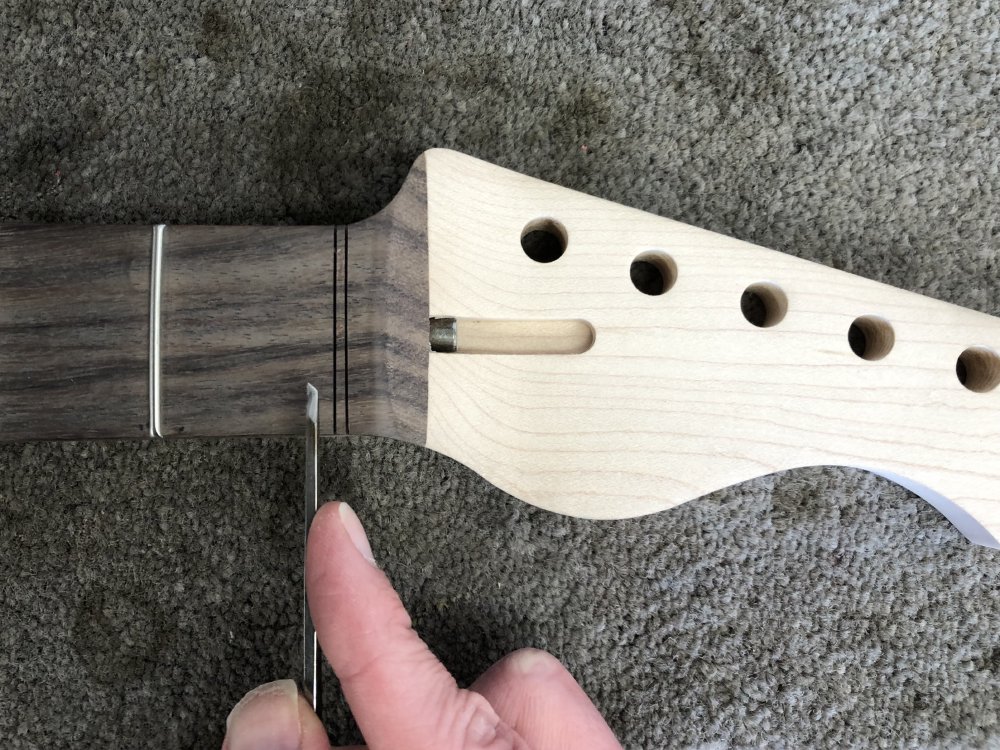
With that done, both necks now just need to have their headstocks laser-etched with some sort of branding, about which I’m still very undecided what to do, as I’ve not found a nice way to use the new MWD branding on a conventional headstock, versus the old Electric Flapjack branding. The best I’ve managed so far is just the logo, and some model text:
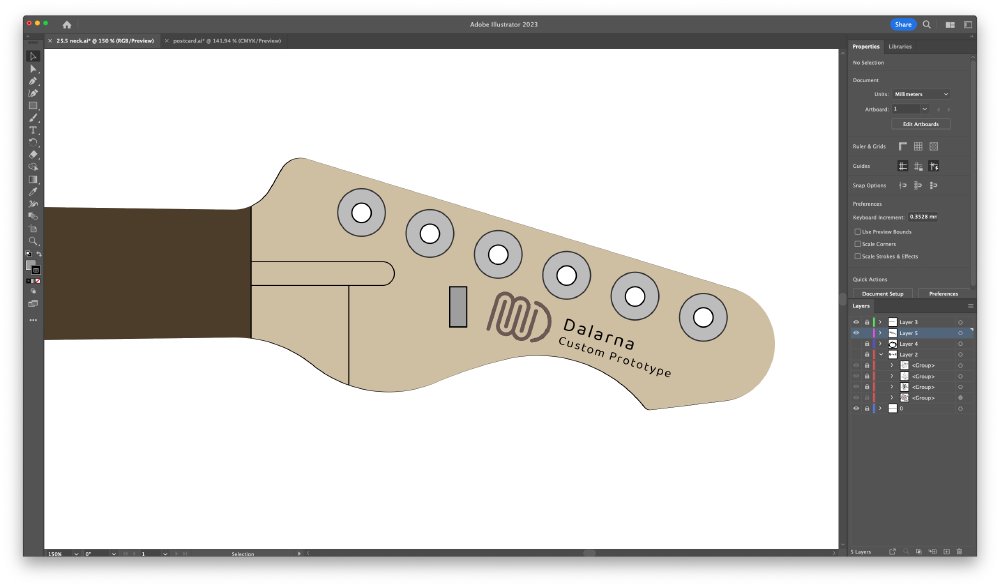
It’s a step back from what I’d wanted to do with having some form of generative art on there, but I feel that right now I just need something otherwise this’ll start impacting my build schedule, and I can always refine it for future guitars.
Getting ready for shows
All of which segues nicely to other branding thoughts. I definitely fall into the common trope of being the creator/builder of things but not very good at marketing themselves, and it’s definitely something I have to engage with more to enable this endeavour to continue.
I’ve applied to have a stand at this year’s Liverpool Makefest, and at some point I’d like to (or rather need to, if I’m honest with myself) try exhibiting in the smaller UK guitar shows: I was due to do my first one of those in March 2020 at Newmarket, but well, we know how March 2020 turned out.
All my leaflets and cards that I have for shows are back from what I think of as “phase one” of my building career, when I was building guitars closely based on existing models, so I feel I need to do a refresh my booth take-aways of that focused on my new direction.
I have to confess I’m not a fan of conference merch/tat, as it feels like you’re just generating landfill, but I also appreciate that having something for people to take away that’s physical is a good way to have them remember you beyond the fleeting moment they’re at the booth, so I need to try and find something that I can give people that I won’t feel will be thrown away immediately. I’ve not been feeling particularly creative, so for now just to get the ball rolling I’ve played around with some designs for things that follow a well trodden path.
First up, is plectrums, which you can easily order online with custom prints:
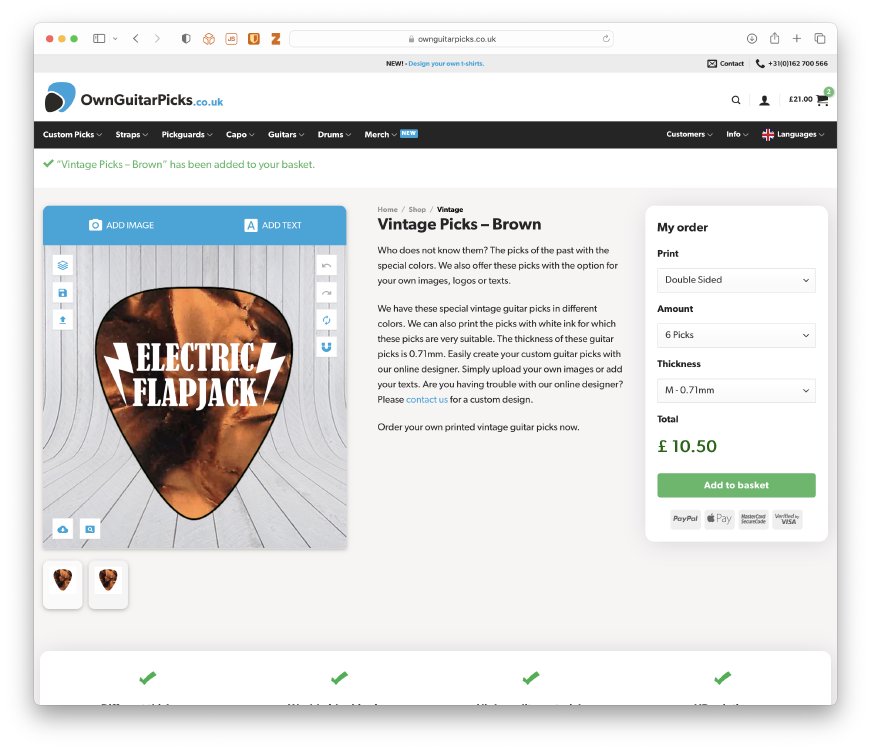
Plectrums are a common swag, and probably wouldn’t help me stand out at a guitar show, but probably will at Liverpool Makefest and other maker events. But again, the challenge there is that as a player I’m very picky about the plectrums I use, as there is both an ergonomic side to them (the ones I use have a grip pattern on them that helps me instantly find the right place to hold them), and a tonal impact (the softer or harder a plectrum is will have an impact of how the string rings out when plucked). So I am concerned that I’m again just making something people won’t use, but chatting to other players I get the impression that they do use them, so who knows. And if I ever reach into my plectrum pot at home for a spare when I’ve lost my favourites (aka, they’re in the pockets of my trousers in the wash), it is usually a branded one I pull out.
Regardless, something here is probably better than nothing, so I’ve ordered a few test plectrums from an online custom plectrum service. I was at least pleased with the site I used that they both offered interesting colours, like the faux-tortoise-shell one in the screenshot above, as all the other ones I’ve seen are either black-on-white or white-on-black, so this should be a bit more distinctive. Also, they do have a gripped option (alas, only over white), so I ordered some of those too, as I really do prefer a textured plectrum surface.
The other thing I started to do was mock up some new flyers:
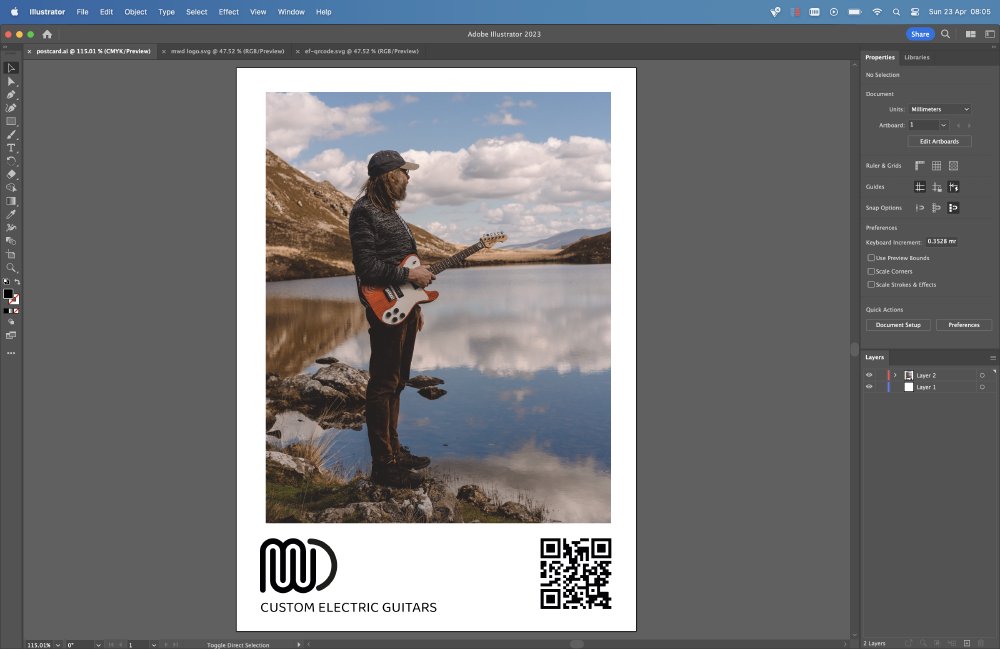
Alas, I’m holding one of my older guitars in that picture, but it’s at least a striking image, and the headstock shape is that of my newer builds. If only Älgen had been ready by the time I went to Wales :) My thought here is striking image on one side, a some text on the other about what I can do custom build wise. That’s going to be the hard part, as I’m not very good at writing short, to the point, but enticing prose.
Chewing the cud
I’ve been continuing to listen to the back catalogue of the Wong Notes podcast by Cory Wong. I find this particularly engaging as a guitar podcast because it’s less directly about guitars as things, but rather about the music they make and the musical process. Cory Wong is a successful musician/guitarist in his own right, so when he interviews guitar players the conversation focuses much more on things like “how do you structure a melody” or “how do you deal with sitting in with another band when invited” rather than just being about “what gear do you play” and “tell us how you got into guitar” that seems to otherwise dominate the genre.
This week I was particularly taken by the interview I listened to where he interviews Steve Vai, who is one of the guitar greats, yet someone I’d never really listened to because of my association of him with 80s hair metal, which is totally selling Steve Vai short (I didn’t realise before this he was in Frank Zappa’s band!). It was an interesting conversation, and afterward I went and listened to both his latest solo album and what he described as the work he feels was where he felt he came together as a solo artist originally. The earlier work I fear suffers from the same problem with listening to Led Zepplin today: you can’t unhear all the music you’ve heard since that work came out, so you can’t quite appreciate how novel and new it was at the time, as it’s been since copied and imitated so many times. But his latest work was quite interesting, even if not to my tastes - it’s always good though to explore outside your regular listening habits as you never know what you might discover.
The other reason I’m aware of Vai is because he’s had a signature guitar series, the Ibanez JEM, that’s been going for over 35 years:
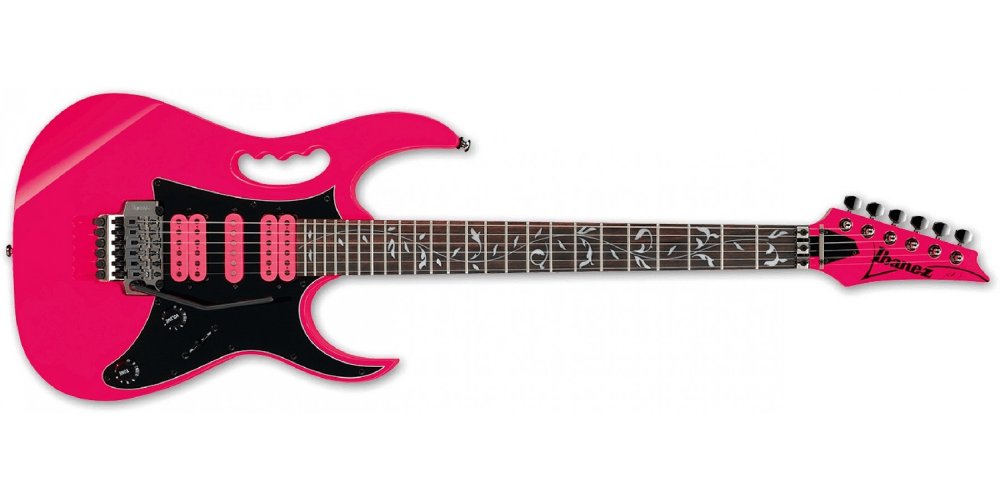
I take some solace in the fact that the JEM’s enduring popularity despite having a floyd-rose term on it means people clearly can cope with difficult to setup/tune guitars (given Älgen’s weird tuning setup compared to a more traditional guitar).
Whilst down this rabbit hole I did discover this other lovely guitar Ibanez make, which is the signature model of Tim Hensen of Polyphia (one of their latest songs features Steve Vai, which is how I ended up here):
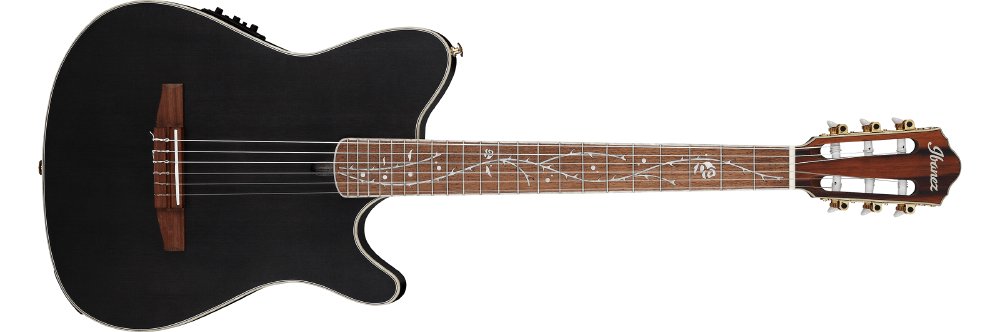
What’s interesting to me is that it’s a nylon-strung electro-acoustic, so seems to play more like a classical electric guitar than a traditional steel-strung electro-acoustic. The photo I nabbed here doesn’t really do it justice, so if you’re interested have a click through the above link. I’d love to give it (or something like it) a try - I don’t think I’ve really ever spent any time with nylon-strung guitars, and yet here it is being put to use by a prog-rock/math-rock band:
Polyphia are good, but not quite my cup of tea generally, but they did remind me a lot of Rodrigo y Gabriela of which I am a fan, which until just now I’d not appreciated are also playing nylon-strung electro-acoustic guitars:
Clearly this is another sub-genre of guitar I now need to learn about: so many amazing instruments out there that I’m yet to play!