A week in the shop
Published 28 Apr 2019
This week I made a start on the body for the first of my Corvette model guitars. The corvette is loosely inspired by the Fender Mustang design, but made more modern/angular, keeps my ergonomic preferences around comfortable shaping, and has a design that reflects some changes I want to make to make building guitars easier: namely making it easier to do test setups as the build progresses without marking the wood, and reducing reliance on tools that I either don’t have at Makespace (e.g., a table router) or are sufficiently troublesome that I want to stop using them (e.g., the CNC Router).
The finished guitar will hopefully look a little like this:
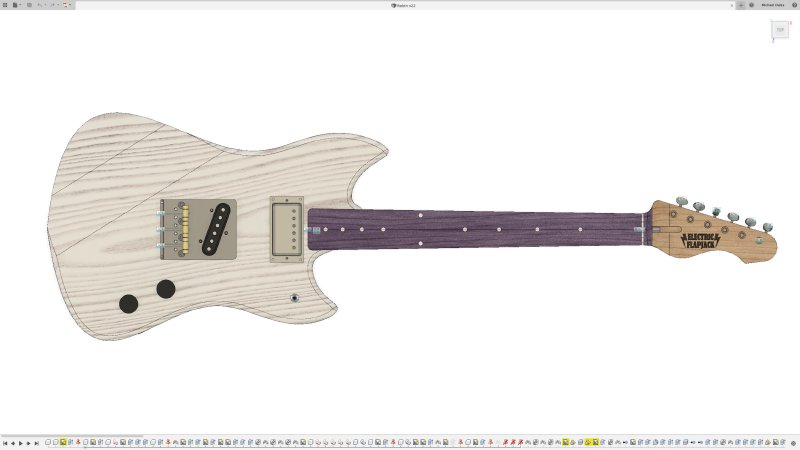
Overall this move away from such tools will mean more hand building, which will be a good step for me I think. Although this makes the guitars more expensive to build, I’m not yet at the point where scaling them in time is a major issue, I’m more blocked on my own ability to operate without the support of the CNC machinery I’ve been using. I’m trying to break a major hangup I have about woodworking coming from the digital realm as I do where everything is perfectly quantified; something the CNC Router in particular has solidified in my technique, and why I’ve been so slow at guitar building because the one I have access to has been unreliable.
On an electric guitar there’s actually very few measurements that need to be near perfect: the position of the nut, the frets, and the bridge are the only things that matter to any high degree of accuracy, everything else is fungible. But because I’ve come from a digital background, and I design all my guitars in CAD first, I have this mindset of wanting every measurement to be near perfect when that’s not actually the case, and I get overly hung up on any slight deviation when building.
I do have one major part where that’s not true: I hand carve the necks, a fact of which I’m quite proud. This was forced on me as I didn’t have the CAD skills to model the neck properly, and as such I accepted that this was a more analogue process, and found that it worked. I just need to do that more, and hopefully this guitar will teach me some of that.
So, having done all the planning, I started making wood dust on this guitar this week. The body blank was roughly the right thickness, but needed taking down a little more. Makespace doesn’t have a planar thicknesser machine, so normally I’d use the CNC Router as a slow alternative, but that’s also playing up again, so I went old school and broke out the hand planes!
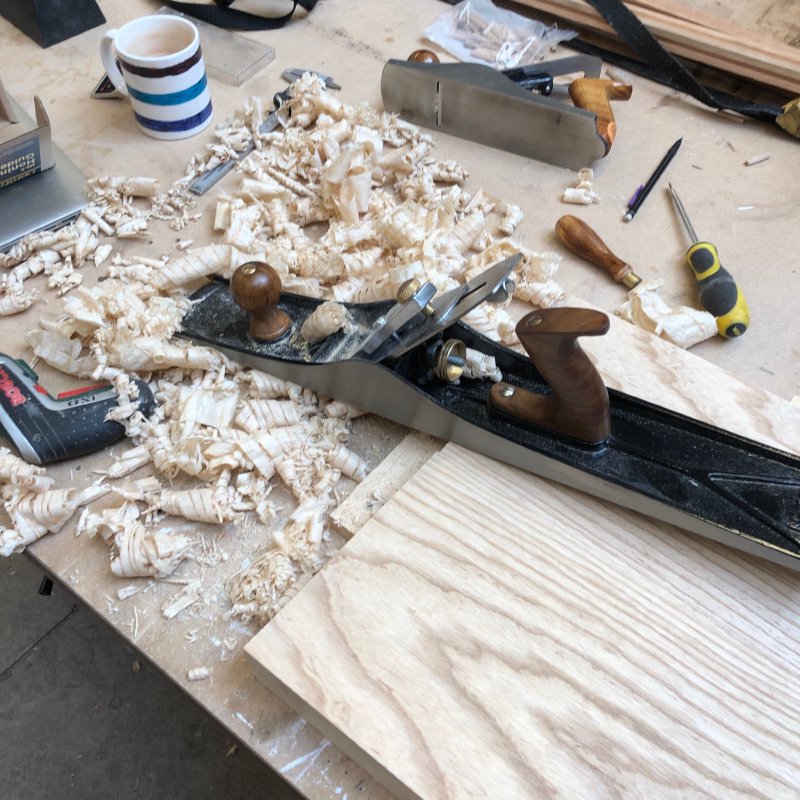
The large No 7 is ideal for making large straight edges, and I had the shorter No 4 there just to get things into rough shape where needed as it’s an easier tool to handle. Now that I’m better educated on setting up a hand plane and keeping the blade in good shape, this went quickly, though does require a reasonable bit of muscle compared to my usual alternatives - free exercise!
Once the body blank was down to the final thickness, I stuck on the template I laser cut previously, and set about removing the bulk of the material using the bandsaw. Although the template is there to let me use a hand router to copy the profile from the template into the wood, the hand router is more a finishing tool rather than a bulk removal tool, so you don’t want to use that from the start, you want to get things close to the template using another method. A well set up bandsaw will cut through the 42mm of swamp ash I have here nicely, and actually did a good job of following the curves of the template better than I expected.
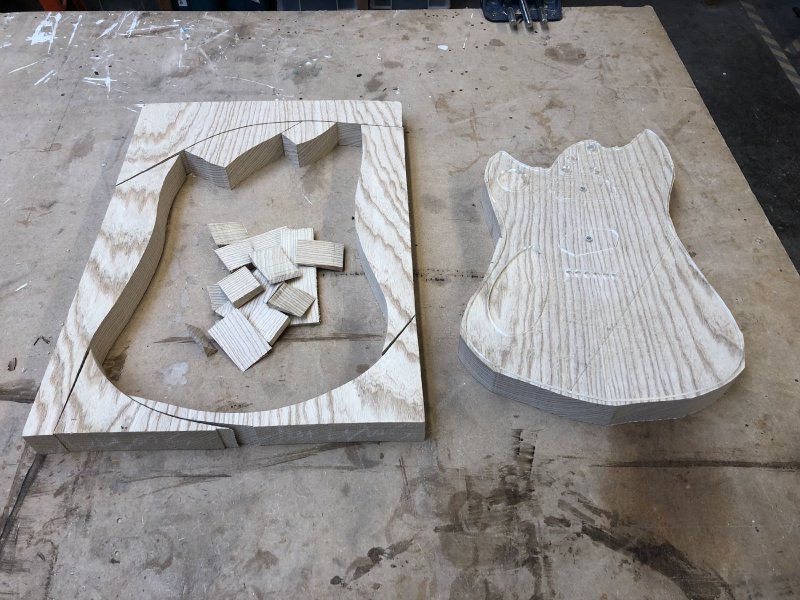
One thing I failed to anticipate: now much dust is made by the bandsaw. Whilst I was wearing my safety glasses and ear defenders, I didn’t protect myself against the dust. The dust extraction system was temporarily out of action in the workshop, and I didn’t consider how much dust a bandsaw makes, and regretted not wearing my face mask for this. Don’t make my mistake: if you’re doing a lot of bandsawing like this, make sure you have good dust extraction and/or wear a face mask.
Once the rough shape was cut, then I took the hand router and made a lot more dust, this time properly protected (ears, eyes, and mouth/nose all covered).
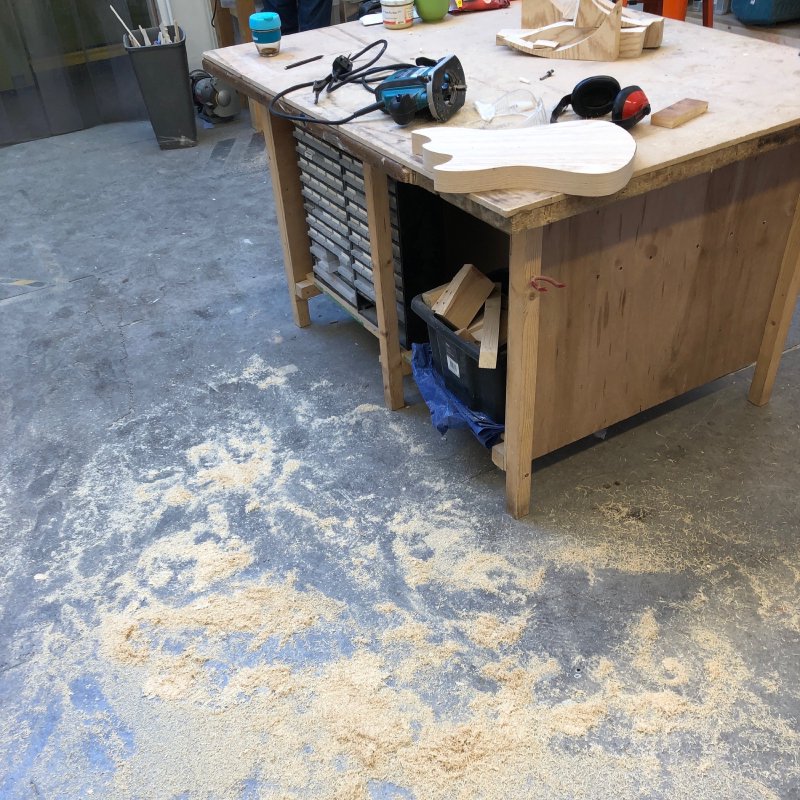
I have a reasonably deep follow bit (with a 1” cutting blade) for the hand router, so this was just a two pass process: once with the template on, and then a second pass with the template removed and using the first pass as the guide for the bit to cut the lower half. The finish this way is pretty good, but there was a slight seam between the two passes, so I broke out the spindle sander to get the outside nice and smooth.
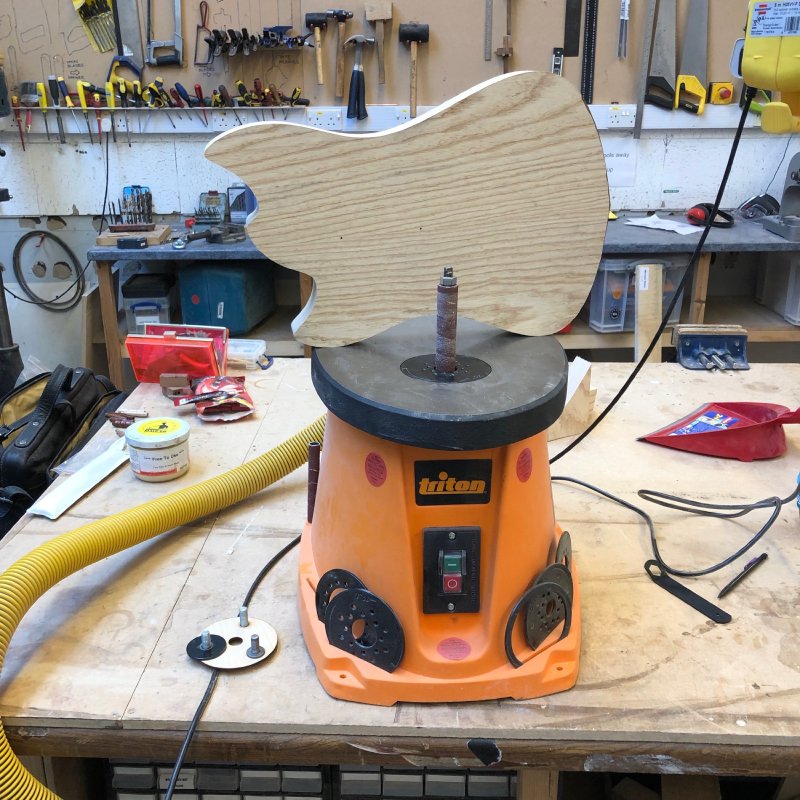
Now that the rough outline was done, the next stage was to make the neck pocket. For this I had a second template, which was designed to use the mount holes from the first template to give me close to perfect alignment (this is part of making sure the neck is straight to the body, so again one of the few bits that does need to be reasonably accurate).
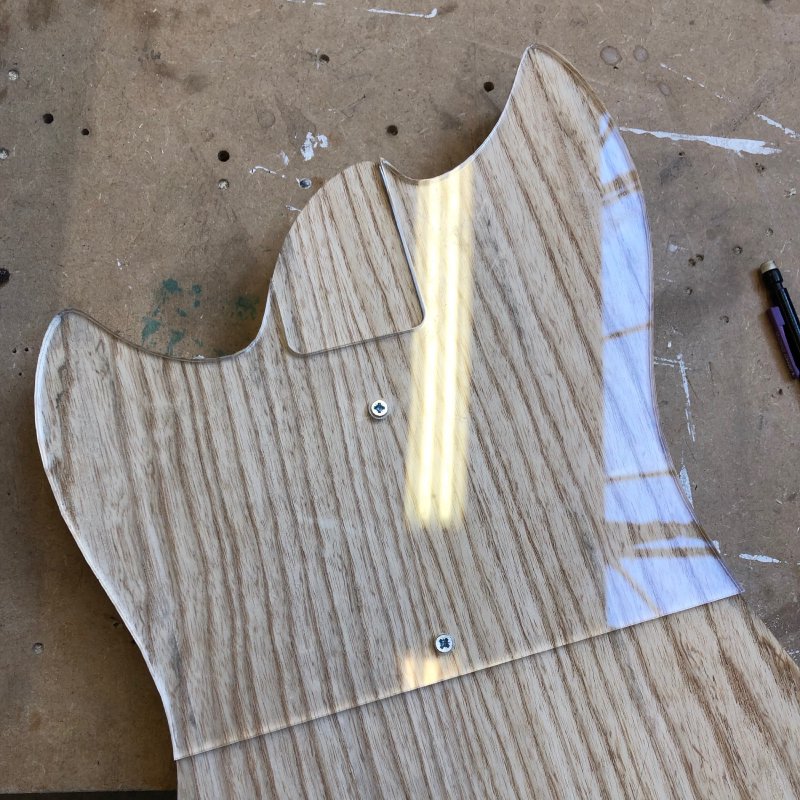
I then marked out on the side edge with a pencil the correct pocket depth (using the join seam between the two halves of the body as my reference line), after which I drilled out a bunch of material before taking the hand router to cut the pocket (remember what I said above: the router is a finishing tool in general, so drilling is a nice way to get rid of some of the bulk).
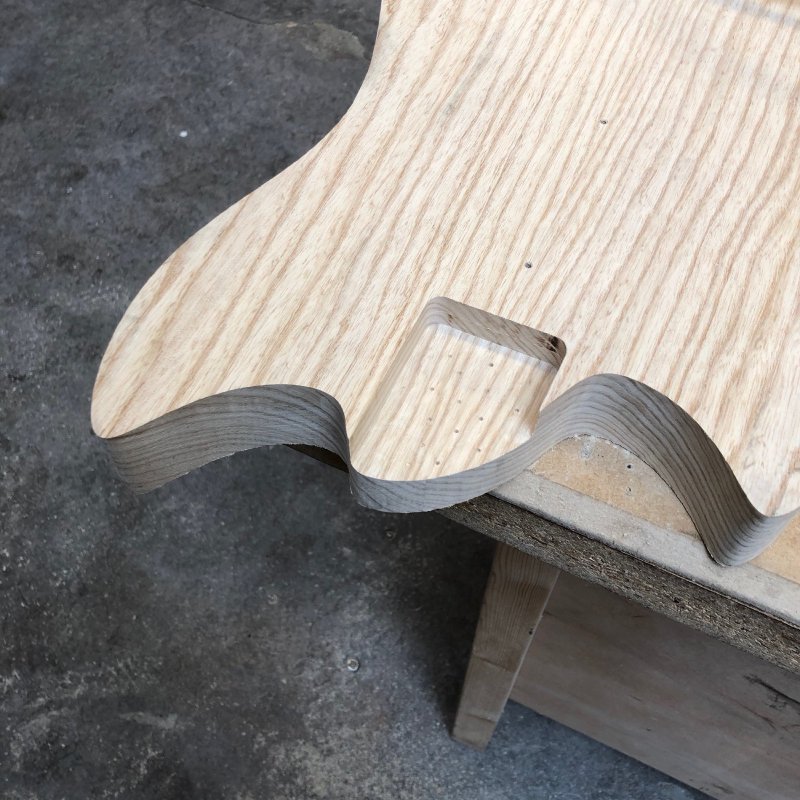
Very pleased with how it turned out (the dots you can see are from the drilling, but these will be covered by the neck, so no one will ever know but us).
Speed wise this entire process probably took a couple of hours, so I think this means I’m just about as fast as the CNC Router Makespace has.
The next stage will be to make the neck so I can get a reference from that for the bridge, after which I can cut the remaining cavities in the body for the pickups and controls. To make the neck I first need to get the maple plank I have down to the right depth, and for that I need access to a thicknesser, so I’ve made an appointment next week to go visit my friend who was one.
I continue to use the fuzz pedal I made as a platform for understanding shipping products. This week, packaging - how would I ship the pedal to people if I made them in small numbers?
I had a bunch of nice wooden boxes from House of Tone, who make the pickups I use, ship their pickups in. They’re very nice boxes, so I’ve kept them to try and find a use for them, and it turns out they’re almost a perfect match size size to hold the fuzz pedal I made (with some bubble wrap). The boxes come branded (as in, branded with an iron), so I took one and sanded it down to remove the logo, which then meant I needed to sand off the rest of the finish to make the box look uniform (HoT relic the boxes nicely, so the sanded top looked very odd on its own). I then laser cut my own logo into the sanded box.
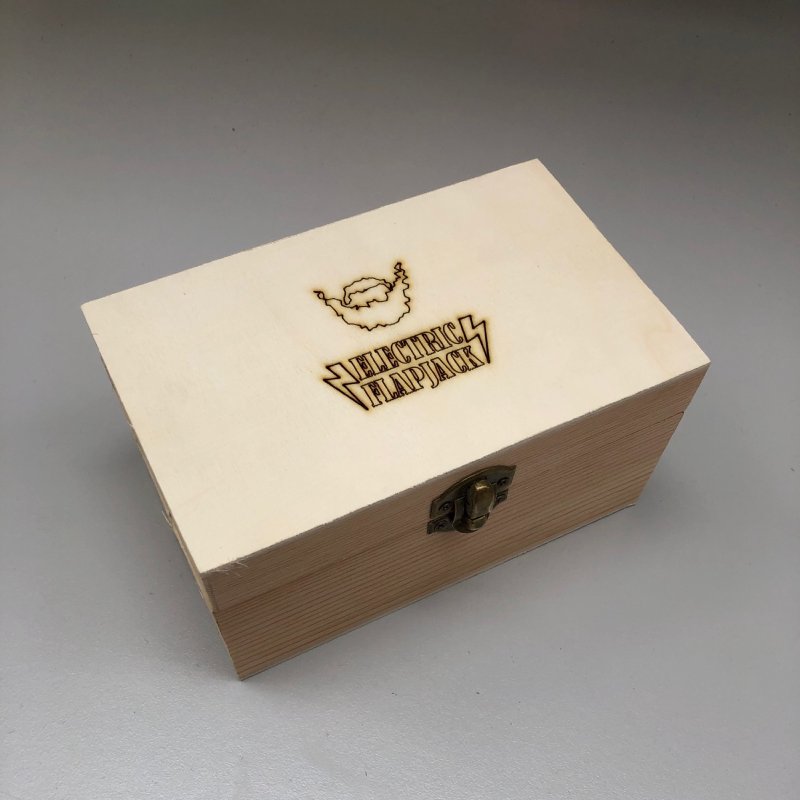
This looks quite nice, and matches the aesthetic of the pedal somewhat. Unfortunately, it didn’t scale as a process: the two other boxes I had didn’t come out so well, either the ply wearing unevenly, or the stress of sanding causing the boxes to come apart (they are, after all, just lightweight packaging, so not the most robust of things). Still, as a quick experiment, I was pleased with the result: at some point I need to ask Matthew whether they make the boxes in house, or if he has a supplier he can recommend. I could make my own obviously, but I already have too many projects on the go, and so that doesn’t scale.
On Friday I also did a bunch of workshop maintenance: replacing the belt and disk on the sander, and sharpening my set of chisels and the Makespace No 4 plane again.
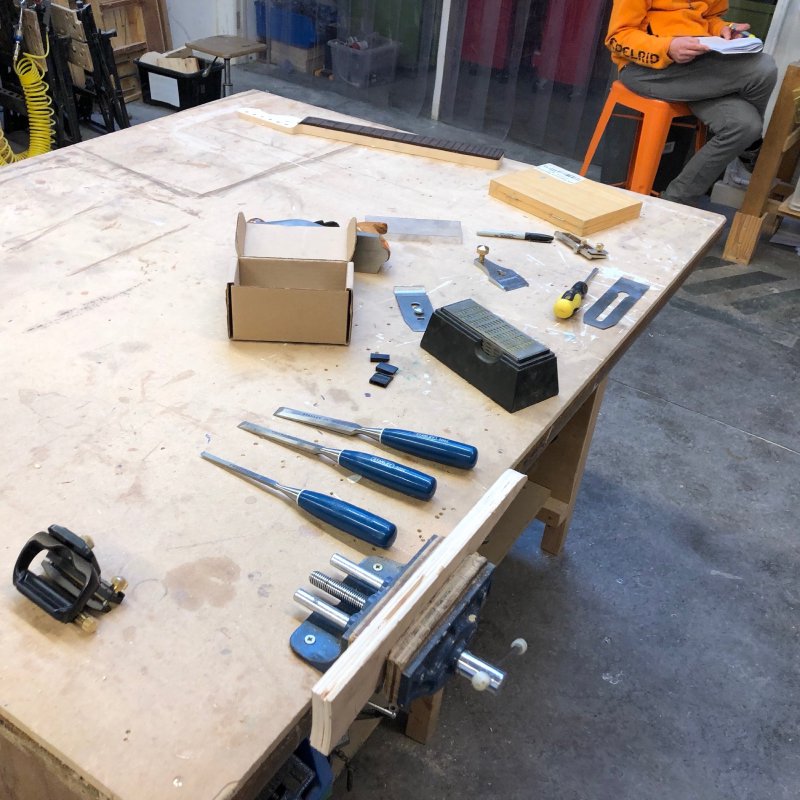
There’s now a set of people who are supposed to help look after the workshop, myself included, and I’ve been trying to find a way to make sure things don’t fall between the cracks as different people respond to different requests that come in via different methods. I think I’d like to follow the example set at DoES Liverpool (as explained by Adrian at last year’s Festival of Maintenance) and get at least the workshop part of Makespace using a software projects style issue tracker to make something that everyone can access that shows what needs to be done, what is being done, and who’s doing it. I just need to see if I can convince the others that this is a good way forward, or find a better way, as the mix of email and one-on-one conversations we have right now doesn’t work well (at least for me).