Two weeks in the shop
Published 28 Apr 2018
Tags: bridge, effects, fretwork, hoxton, mastery, owl, pedals
I missed last week’s update due to a quick visit to the Isle of Skye for my sister’s wedding, which meant a slightly shorter working week last week and this. I did use it as an opportunity of going past Glasgow to deliver the Red Rocker guitar to its owner at last, which was nice. Still, I did manage some shop time over the last couple of weeks, so here’s what I did.
The prototype offset guitar is coming along. I did the fret work on the neck, getting the frets levelled and polished, which took an entire day. With this build I’m trying to keep track of where time is spent on a build, allowing for the fact that I’m still learning as I go. But frets I’m kinda used to now, and I suspect this is par for the course.
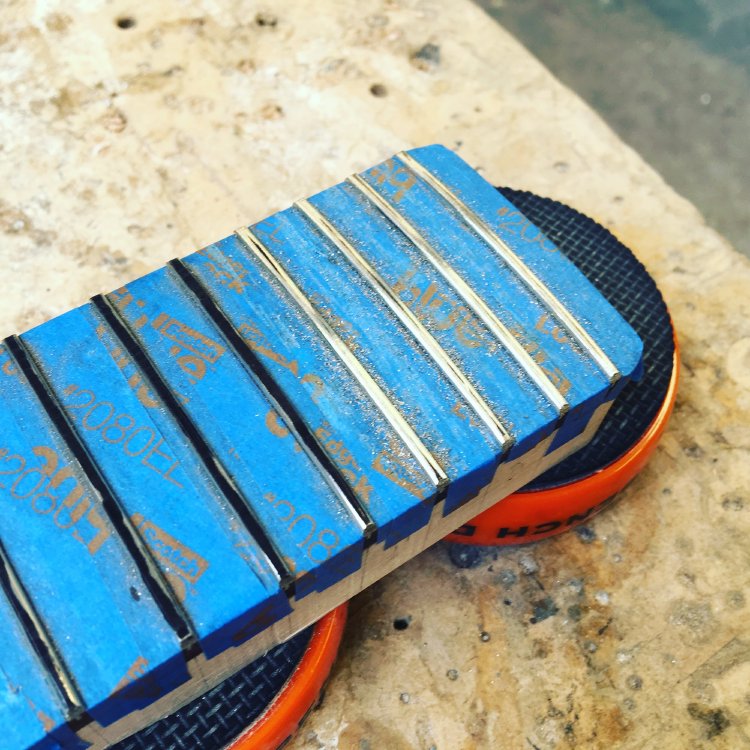
I also spent a good chunk of time sanding the body down. My theory is that every finer grit level of sand paper only exists to show you imperfections in the sanding you did two levels back. It’s amazing how you’ll think you did a great job at 120 grit, getting the tool marks out, and then by the time you get up through 240 grit, it still looks good, but then at 400 grit there’s suddenly a bunch of tool marks showing again! So then it’s back down and up again through the grits. It’s tiring work, but time invested here will pay dividends in the final finish.
As I mentioned last time, my aim was to get this prototype strung up (at least partially) so that I can have confidence that my offset design (which although based on an existing popular guitar, is my own CAD design) hangs together right. I finally got the last of the bits for this guitar, a Mastery bridge unit, so I was able to sit down and put some strings on it.
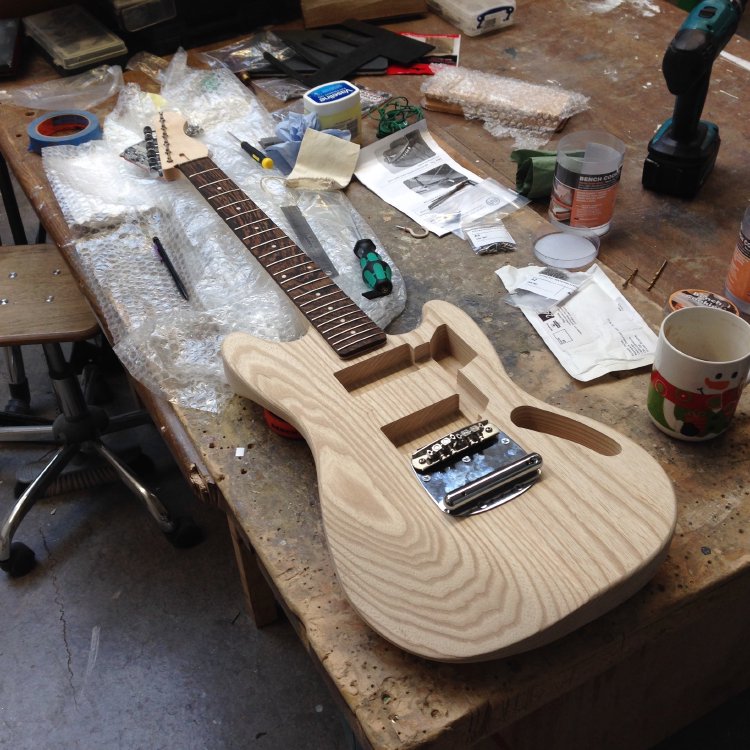
It all seems to sit together really well. Now I’m happy with this, I can next week start cutting the wood on the two commissioned offsets I have, which is a great relief. This one I’ll continue to polish up and finish as the others go along, but right now my priority will switch to getting the other guitars moving.
Whilst waiting for parts to be delivered at the end of the first week, I did finally sit down and write some code for the OWL effects pedal I got recently. The OWL pedal is an open source hardware project that lets you write your own effects code and load it onto the pedal. Lack of time had meant that despite having it a couple of months I’d not tried anything yet, so I used a spare couple of hours to correct that.
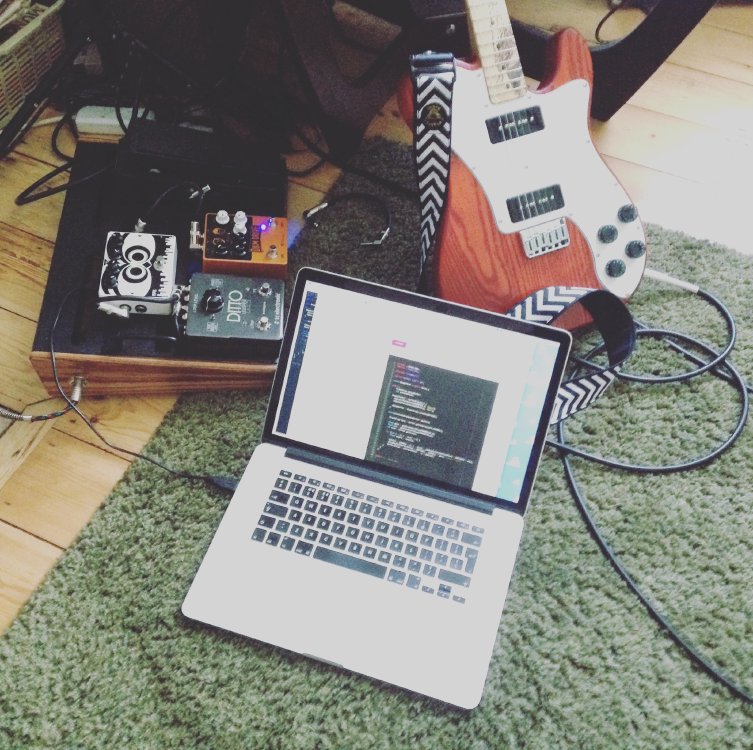
I wrote a simple, but complicated, echo effect as my hello world program. Echo effects are fairly simple to write, you just need a memory buffer into which you write the sound as it comes in and then read it out later based on some delay. You can of course play with this, and vary things like how much signal you blend back in (how loud is the echo) how long the delay is (who quickly you hear an echo) and then how quickly the echo decays. I mapped a bunch of these to the dials on the OWL, and in the end I could come up with quite an array of sounds for not much code. I can even lock in a sound almost like a repeater, though without a button to map that to it’s not very practical.
The code is on github if you’re interested. I have to admit I was inspired a little on this by the Echorec video by That Pedal Show, which was the first video of theirs I ever saw, and in the end I just used my effect to badly play Pink Floyd riffs :)