A brief week in the shop
Published 24 Aug 2020
A short update this week, as I was mostly travelling to visit my family up in Scotland, which meant very little shop time, but I did get to see some nice scenery where I could start my day by making fresh coffee on my camping stove in places like this, at the head of Loch Long:
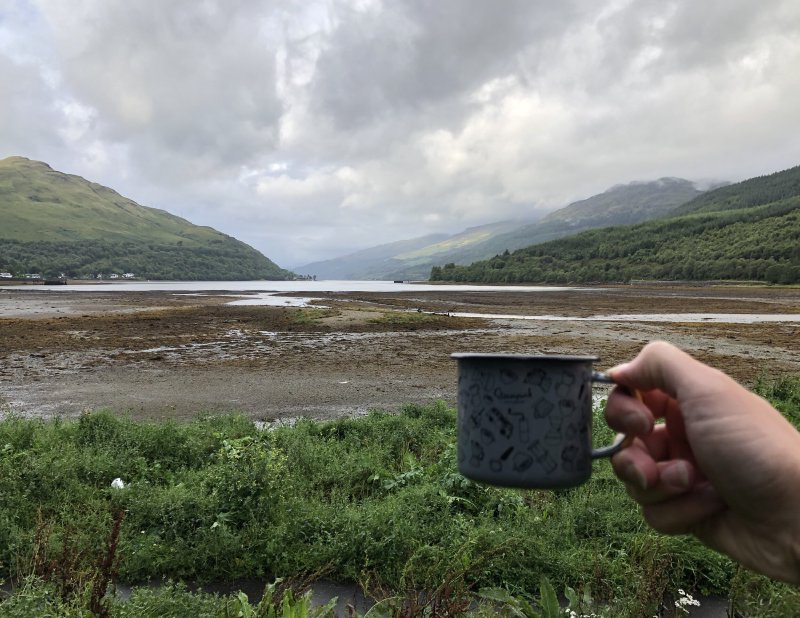
I rushed break, but it was nice to see both my family and the landscape I still think of as home. Also, the trip helped me play more guitar that I have done of late by causing me to pick up a different instrument…
We have an electric car, and not one with a very large battery, which means every 100 miles or so I need to stop and top up on electrons. With modern fast chargers that doesn’t take too long, probably about half an hour per stop, but that’s long enough that you want something to do to pass the time. Thus one of the top priority tasks I had in the workshop last week was to fix the broken bridge on my cigar box guitar (a regular guitar being a bit too large to comfortably play in the car).
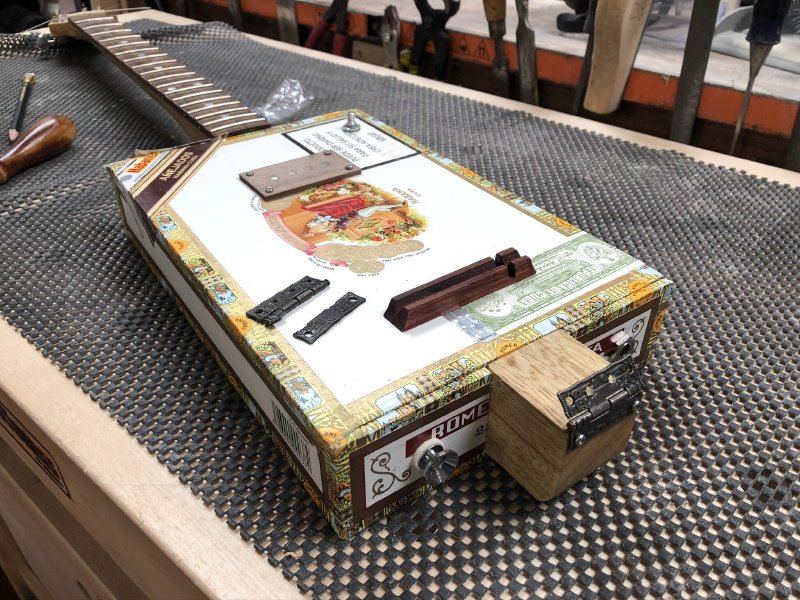
As part of its rustic charm, I used a jewellery box hinge to anchor the strings at the tail of the guitar. Which was fine, until my guitar teacher encouraged me to move up from tens to thirteens (thicker strings being better for slide) and the hinge decided that this was all a bit much and sheered.
Given lack of time to come up with a radical new alternative, and given I had spare hinges, I just refashioned a new bridge similar to the old one and put the lighter gauge strings back on for now.
This held fine, and I was able to pass the time on my journey watching Justin Johnson cigar box tutorials on you tube and trying to up my slide game a bit. Given its size, a cigar box guitar makes a perfect travel companion. I took my small Blackstar Fly practice amp with me, but I didn’t use it: I’m constantly amazed at how loud a cigar box guitar is naturally even without sound holes.
I have enough wood left to make another one, so if you fancy something like this let me know. We’d just need to select a cigar box or other similar sized box that would suit your tastes.
With that sorted, I returned to the body that I started on last week, getting those wings for the lower bout sorted.
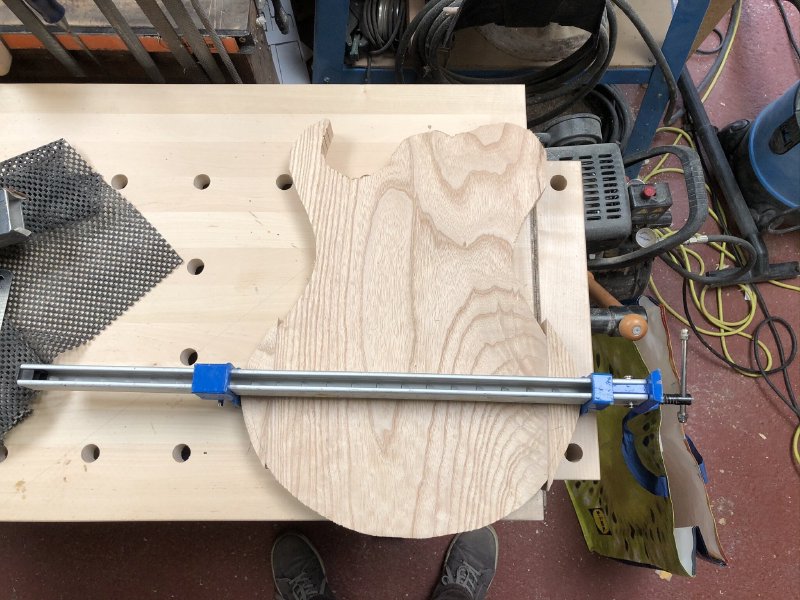
To get the two surfaces ready for gluing I had to hand plane the edges nice and flat. The poplar was a bit of a pain for this, as it really wanted to tear no matter how I planed some of it, but with some patience and a very shallow hand plane setting I got there in the end:
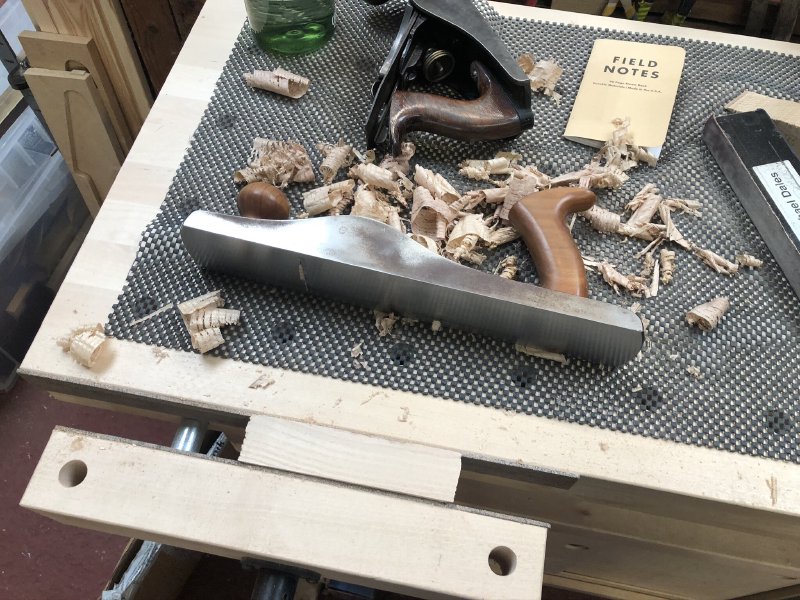
With that done, I glued it up and left it for resumption this coming week, where I’ll start by trimming both the body and neck flush with the hand router.
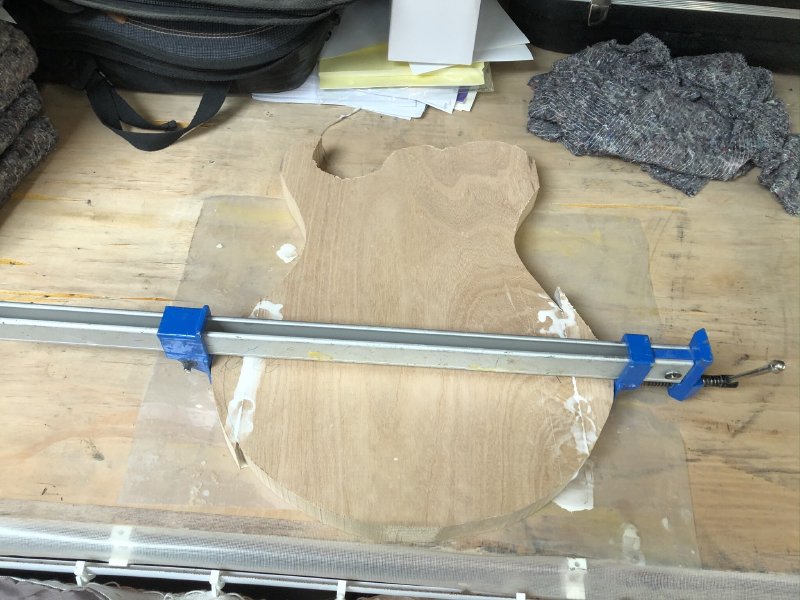
The only other related thing was on the way home I stopped by MAC Timbers, up near Peterborough who were having an open day (and indeed their last open day was where I got the Poplar for the above body from). Usually MAC Timber aren’t just open, being a small lumber yard, you need to make an appointment; so the open day was a good chance to have a look again at the sort of woods they stock.
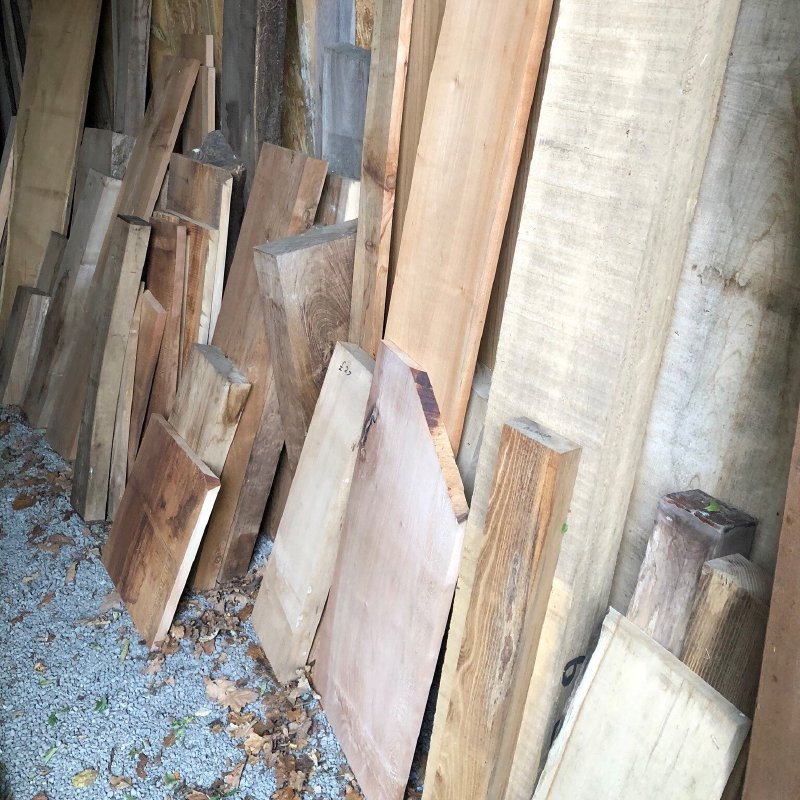
Due to traffic, I only arrived just as they were packing up, so I didn’t see any woods there, but it was useful to chat to the owner Mike about what they had in stock and what was becoming available.
Over lock down I did start to do a little research into what woods I might use for guitar builds that were both sustainable and had low travel miles. I shall try write that up into its own post, but that’s why I was interested in understanding a bit more about what Mike has to offer rather than just relying on the regular luthier suppliers.
Although solid body electric guitars have a lower set of requirements for the woods than say an acoustic guitar, there’s still a set of parameters you need to understand, such as how much the wood for the neck will deviate over time, how dense the wood is in terms of final weight, etc. This trip gave me some motivation to try finish that research and then go back to Mike and see if anything on my list can be sourced reliably and at what cost compared to the usual woods I use.