Another week out the shop
Published 4 Feb 2018
Tags: amp, cheese, monkigras, video
A frustrating week in terms of shop time (I didn’t set foot in it once I think), so no progress on the amp again, but the new transformer has arrived, so I’m unblocked in terms of parts, I just lacked time to move that forward.
On Monday I was feeling under the weather so staying at home and trying to get better. I did use this time along with some of Tuesday to move my CAD design for the next set of guitars close to almost complete:
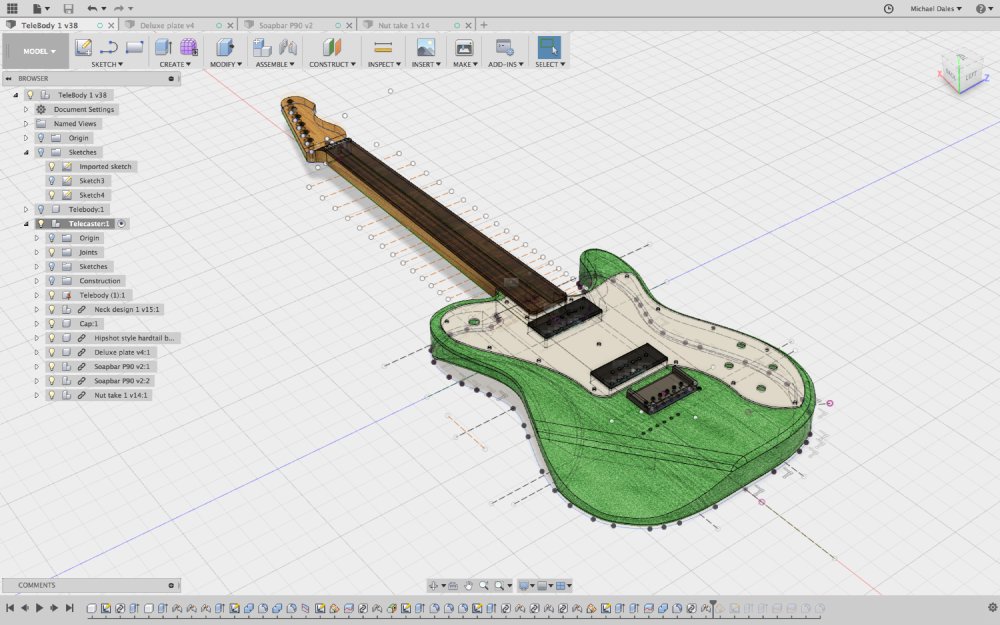
Investing time in my own CAD models has many benefits, not least of which I own my end-to-end design workflow now, so even though this is a t-style guitar, it’s my t-style guitar design, not one I found on the internet or traced myself. This means I can do tweaks and changes design wise that would otherwise be quite hard.
One of the issues I’ve struggled with as a new luthier is getting my head around wood weight and density. As a result most of my recent guitars have been at the heavier end of the spectrum: not quite rosewood tele (a notoriously heavy design Fender shipped briefly), but certainly heavier than I was aiming for. To some degree, this is down to material costs: I’m using regular ash or korina for my bodies, and unless you spend a lot of money to get the very light stuff, you will get the more dense material, and until I’ve made enough guitars to know I’ll justify the cost I’ve been shying away from getting expensive materials whilst I still consider my workflow experimental.
However, even with better wood, weight management is still important. Numerous guitars, for example Gibson’s Les Paul range, use weight relief by carving out some of the body and then using a cap piece of wood for the top (which is also an excuse to use a prettier bit of wood on the bit people see, and a more affordable wood for the bulk). Another approach is to make a semi-hollow electric, where you have a body cavity and an f-hole to get some acoustic properties, like the Telecaster Thinline or many Rickenbackers.
I quite like the idea of doing a semi-hollow guitar, but having hollow cavities in the body means you have to be careful with the comfort carves that I like to do, whereby you scoop out the back of the guitar where your belly makes contact with it and on the top where your strumming/picking arm would rest. There’s a real risk that if you’re not careful carving these scoops out that you will carve into the body cavities and end up with a guitar that looks like a bit of swiss cheese.
The solution to this is, as ever, measure, measure, cut, and modelling everything in Fusion 360 lets me do that. I spent some time this week designing not just a regular t-style guitar, but one with cavity placement to make it semi-hollow or just weight reliefed depending on customer preference, but also with the scoops factored in so there’s no risk of adding holes where I don’t want them.
Having completed that design, I’ve also been understanding the options in fusion for taking this more complicated design onto the CNC router for the initial roughing out stage. This means not only will the CNC router do a 2D cut of the body outline for me as I’ve done in the past, but it should also rough out the cavities and the areas where the comfort carves will be, ready for me to then hand finish it without risk of taking material out of the wrong place.
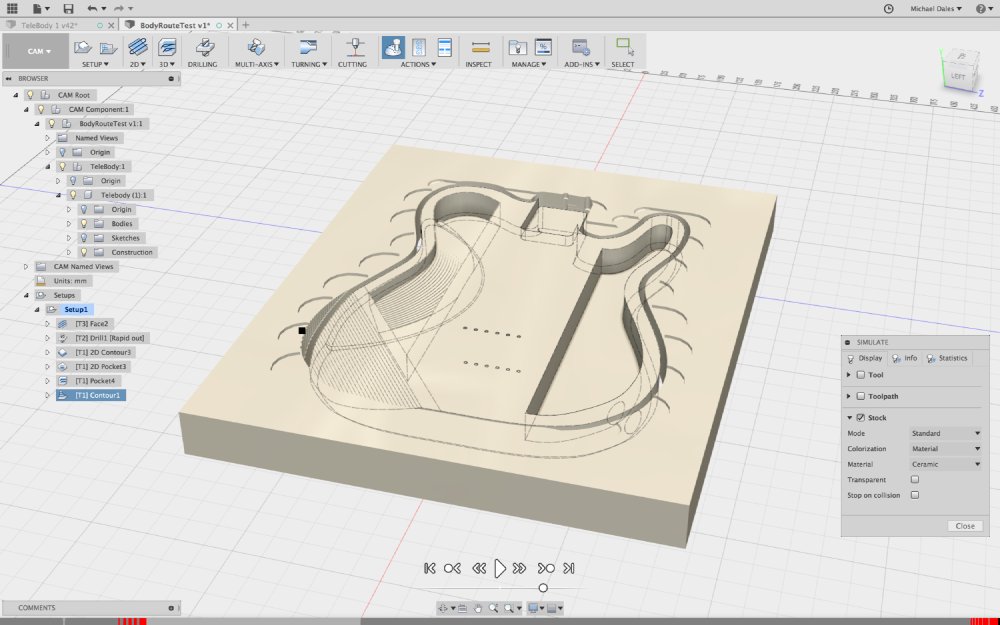
The next step of this will be to actually get some wood and make some bodies to test it! To this end I’ll shortly be announcing pricing on a prototype run, whereby I’ll make two guitars based of the new CAM model at close to materials cost so I can validate the workflow I have. This means my prototypes will end up in a full working guitar, and you’ll get a custom t-style to your specification for a fraction of the regular price. More in the coming days on that, but if you want to get in early drop me a line, as I’ll restrict this run to just two guitars.
At the same time as planning the next generation of guitars, I also booked some studio time and recorded some demo sounds for the two I just finished. In the past I’ve just recorded demo videos at home, but I really wanted to do these two guitars justice without having my neighbours get too upset, so booked a studio with a “proper” amp and spent the entire Tuesday afternoon just trying to film bits of me explaining and demonstrating the features of both guitars #3 and #4.
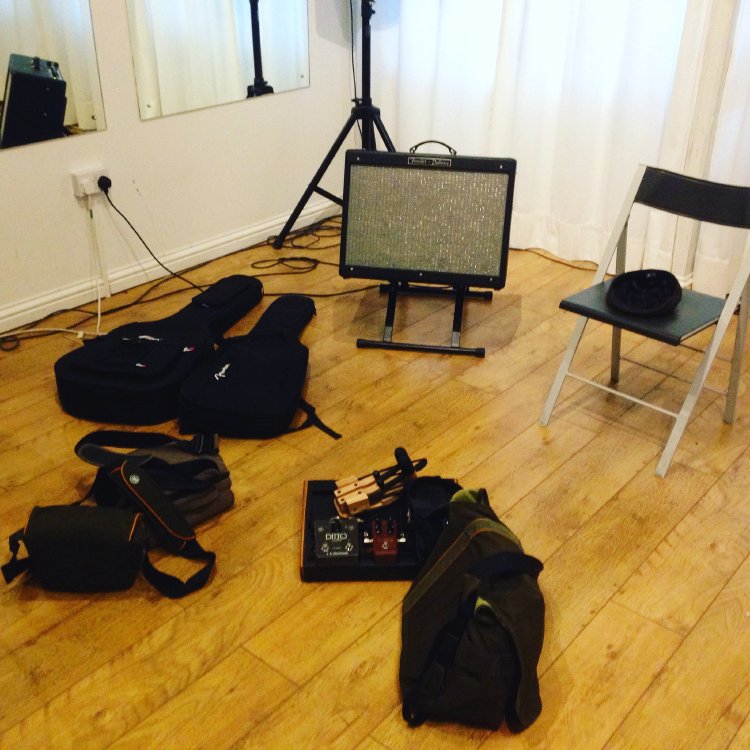
The studio was able to set me up with a Fender Hot Rod Deluxe, which is a 40W valve based amp: a proper gigging amp. It was actually surprisingly hard to tame a 40W amp in such a small room, at least for someone not used to such high output amplifiers: even with a low master volume (just above 2 out of 12) it was too loud in such an enclosed space, but below that the treble was overly dominant and I had to have the EQs set to extremes to adjust for it. An interesting lesson in amp management, which I’ll need to practice some more.
By the end of the day I had 40GB of video and audio to process. I spent a bunch of Wednesday reviewing all of that and documenting where all the bits were in which file ready for editing and then made a start on the first video. I have to say, I am quite disappointed with the footage quality; recording a video on your own with limited time is tougher than I allowed for, and it was only when I got home I realised my camera hadn’t really been set up correctly. However, this has forced me to include more stills in the video, and I think that actually is an improvement over what I originally had planned.
The remainder of the week was taken up with attending Monki Gras, billed as “the developer conference about craft culture”. It’s not a description that makes much sense I think unless you can pin down what craft means, as it’s a term used by many people to mean different things, but then probably no worse than the way the term “engineering” is used in “software engineering”. Anyway, for me it was two days of talks about the theme of building and sustaining projects, not just software/hardware (my professional background when not building guitars), but we also heard from other fields such as brewing and fashion, and how they struggle to make something with care to detail (which, after many talks on the topic, I think I’ve settled on as my definition of craft for now) and both sustain themselves in terms of immediate business and the longer term. All of which possibly sounds a bit waffly, and probably is, but I’m a big fan of going to conferences as places to let your mind soak up a different vibe and see where it takes you. As a starting out luthier the topics certainly resonated with some of the challenges I face, albeit just voiced in a different domain.
It was also a conference that built in time for attendees to talk to each other, and not just listen to speakers, which was quite refreshing. Before each break (other than morning coffee), the break itself was proceeded by a short talk (designed to fit the overall conference theme) by the brewer who’s beer was being served at that break, which was a nice thing I’d not seen done before. There was actual good coffee. There was, and I provide photographic evidence lest you not believe me, a cheese mountain.
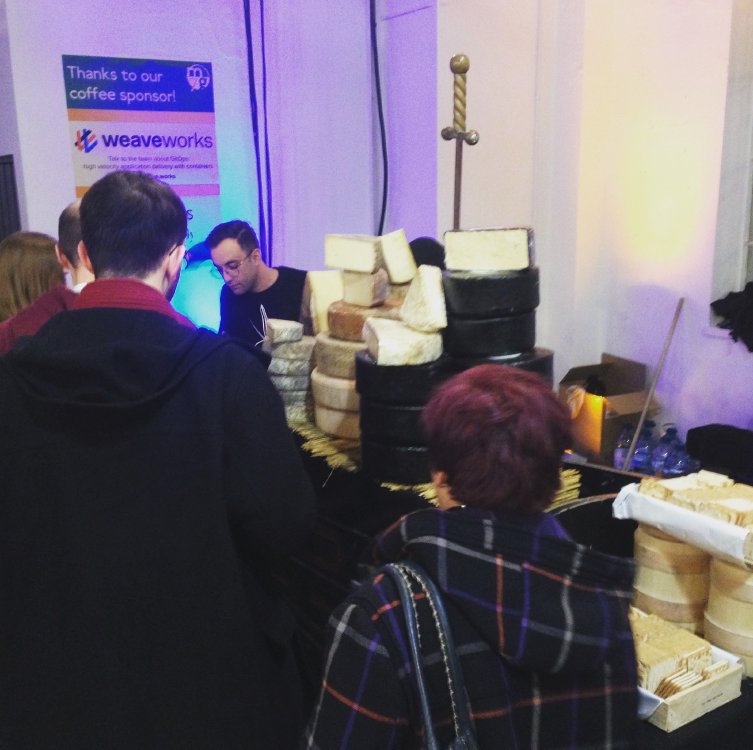
It was also during these breaks that I took to introducing myself as someone who builds electric guitars first, rather than a technologist as I would normally, mostly just to stand out from all the other software people. It was a fun to see people’s reactions and then the conversations it lead to. I still struggle to see this as more than a protracted episode of Faking It, given my 25 years in software and hardware, so voicing that I do this was quite a fun experiment in overcoming yet another round of imposter syndrome.