A(lmost) a week in the shop
9 Dec 2017
Tags: amp, measure measure cut
This week was meant to be about the assembly of the guitar #3 and #4, but I hit a bunch of small setbacks that have pushed things out another week. Whilst I don’t wish to whinge, I think part of trying to document progress is explaining what to do when things inevitably don’t go to plan.
First up, is the lack of standardisation on parts for guitars in terms of sizes. This is something that is in part down to my naivety: you’d assume that if you got part A for a particular guitar and part B for that same type of guitar that they’d just fit together; that after all is part of the benefit of starting out recreating a well known design, to simplify the process in part. But no, you often find this happens:
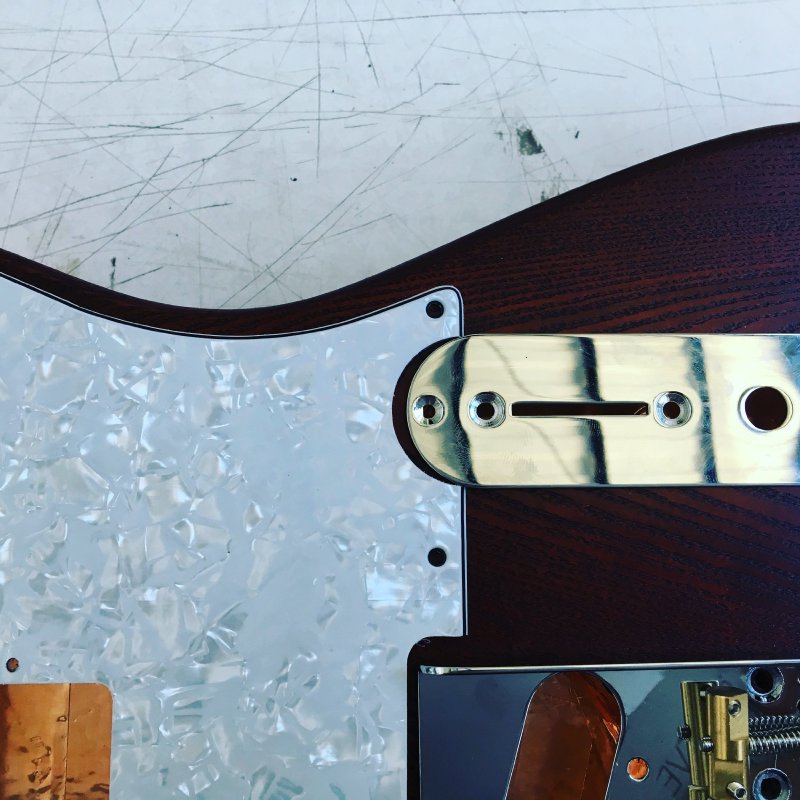
Over time a lot of guitar parts have changed shape subtly, switching from imperial to metric, or just model evolution over time. Unfortunately, unless you are aware of this, you end up with surprises like the above. In fact, that was one of two such surprises I had this week, as on the orange deluxe it turns our the bridge I bought was a few mm longer than the standard too. In both cases a little modification to parts is possible, but for the want of a couple of days it’s much nicer to get other parts that fit and then use the now spares on other guitars. Anyway, as a lesson for any would be luthiers reading this: don’t just measure twice before you cut, measure twice before you order; the only problem being that a lot of parts don’t specify these things, so you do in the end need to learn which suppliers use which sizes and find ones you like.
The other thing I’ll take from this is that I should do a test assembly as early as I can so I don’t find all this out at the last minute. However, the order in which I put things together as I moved from planks to guitars didn’t lend itself to this, so I’ll rework that flow next time.
The other setback I hit was one I documented here a couple of weeks ago: yet another screw split as I was screwing it in:
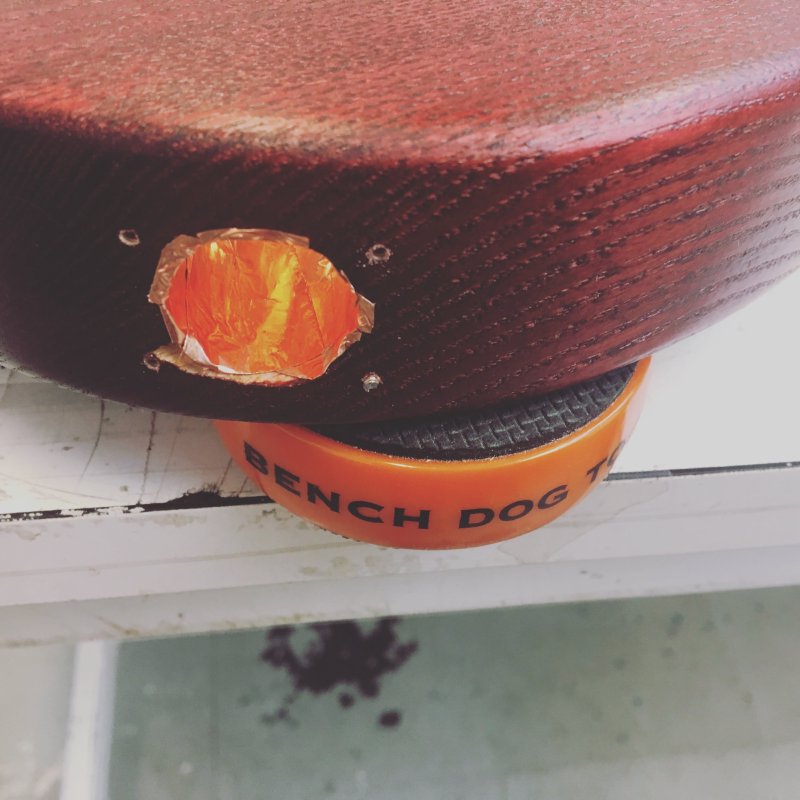
As before this was another 2mm sized screw that came with a part, and I think the lesson here is that the screws that come with parts aren’t necessarily the best, and if they’re very thin and your wood is tough, then consider using screws you know to be good rather than the ones that come with the part (a lesson imparted to me by others now that I discussed this with them). Of course, sometimes things just go wrong, but two in a month smarts a little. I had drilled a pilot hole, I had made it deep enough, and so forth, but it still just snapped. Thankfully, having gone through this once before, I was able to recover it quickly using the same method, but it’s still annoying and still costs me a day as I needed to let the wood glue I use as part of the repair set.
So a week of small setbacks, and a few instances of counting to ten slowly. I try in general to share the positives of progress on the guitar, and I suspect to some degree I make it look easy on my instagram stream by posting all the stages of completion as I go along, but it’s not all plain sailing, and you have to expect the occasional setback. Part of what I like about luthierie is that it’s a very different discipline compared to writing software or designing electronics: you can’t hit undo if you make a mistake, you have to find a way to move on regardless. At times it is very frustrating, but then that’s also in part what makes it satisfying as your design comes to life as a musical instrument.
Onto happier notes, guitars #3 and #4 are close to completion now, and starting to look wonderful:
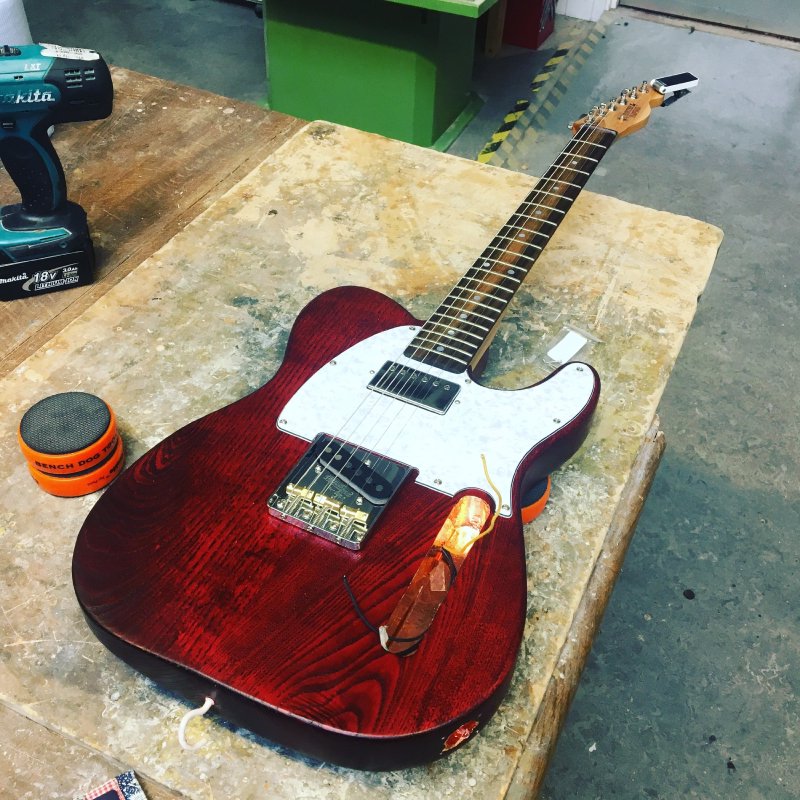
Hopefully next week will mostly be spent assembling the guitars assuming a smoother week than this one.
Aside from working towards the end of the current guitars, I’ve done some more work towards the first amp build. Mostly that has involved a combination of notebook sketching and continuing to learn how to use Autodesk Fusion 360. The build will be a 5W 1x10 combo amp for practice/rehearsal. For those not familiar with all that, it basically means it’s a single box that’ll contain both the electronics and the speaker (a combo), be reasonably quiet (5W is not enough to gig with, but plenty for home and practice use), and it’ll contain a single 10" speaker.
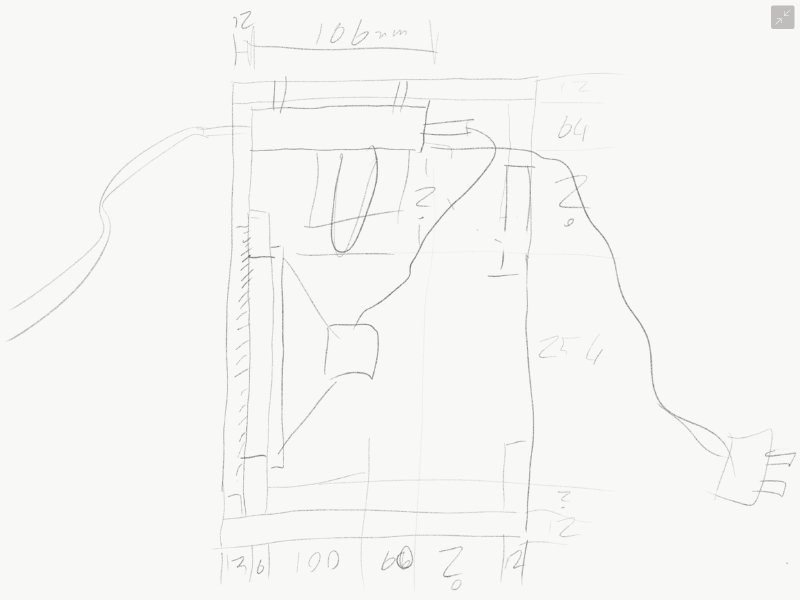
Having got the parts from various sources, the next thing I need to do is design the cabinate to house it in. The plan is to produce the design in Fusion 360 and then produce the panels on the CNC router I have access to at Makespace. To do that I’ve started first modelling both the metal chassis for the electronics (which also has the controls on it) and the speaker. This has been a nice introduction to Fusion 360 before I try building my own bits from scratch.
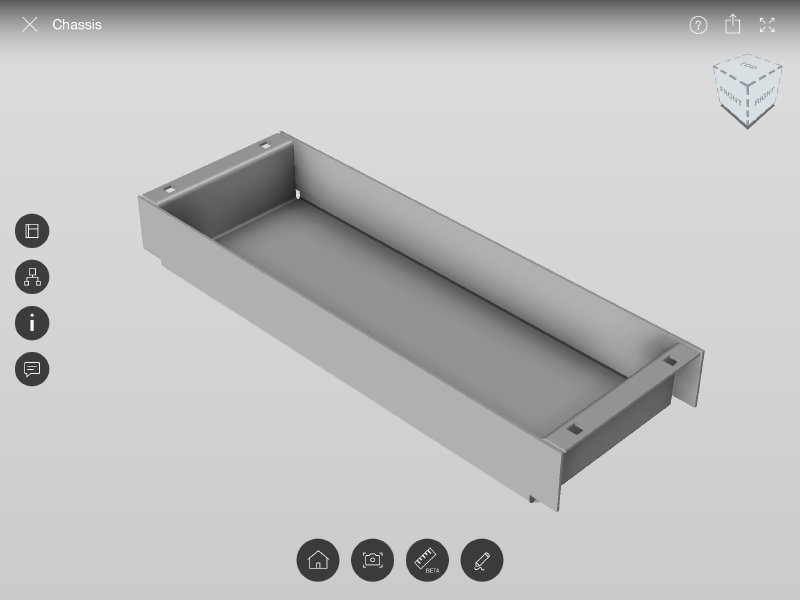
Finally, as guitars #3 and #4 do draw to a close, note that I’m still have the slots for guitars #5 and #6 open, so if you fancy a guitar that is built for you, get in touch. Pricing and timing will depend on what you want: I’m pretty adept at producing t-style guitars now as you can see, but I’m itching to have a go at other solid body or semi-hollow body designs: perhaps an S-Type takes you fancy, or a Les Paul Jr for something a little more raw? Or even something that it’s just hard to get like a baritone or a custom scale length variation.