A week in the shop
Published 24 Sep 2018
Brief notes this week, as I’m keen to press on with things!
To start the week I made the fretboard on the commission offset, just as I did two weeks previous on the recovery offset, the only difference being that this fretboard is made of wenge rather than maple. I did both the cutting out on the CNC router and the laser etching of the fret slot guides.
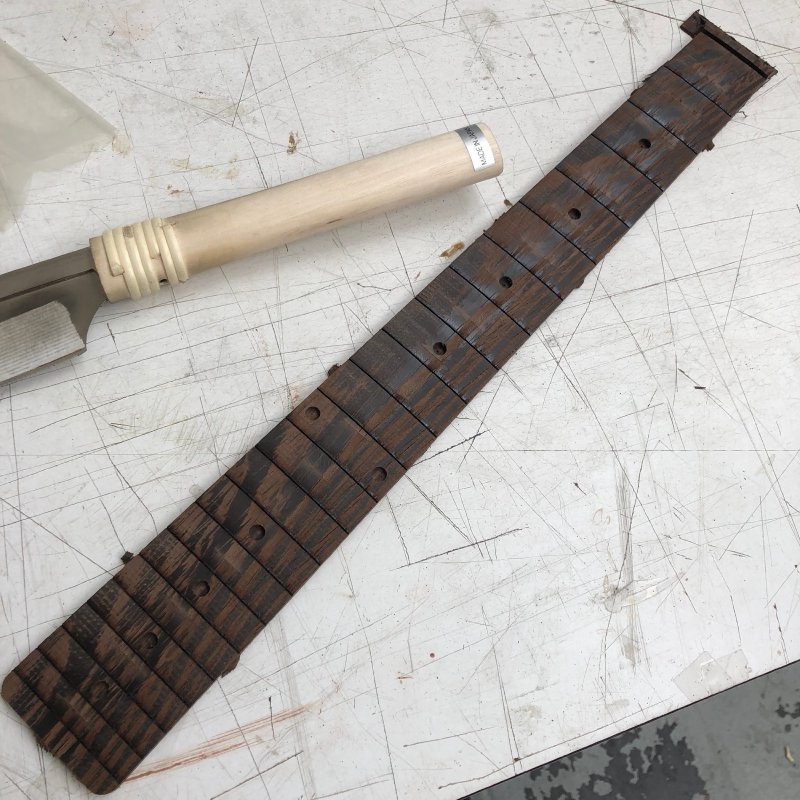
Thankfully for once I was just repeating what I did before, and it all went predictably well. I find one of the things I’ve yet to do is repeat any designs, so most things are always new which I think is part of why I’ve been so slow to make guitars this year. My original intent with the commissions I took in February was to just make some more t-style guitars, to leverage the fact I was building the same again, but in the end there’s been enough change I’m still slowed down by each piece being new to me. Which is why it’s nice I essentially have two guitars being built right now following the same path.
The inlays for the dark fretboards I like to make with clay. I get some air drying clay, set it into the fretboard holes, leave it to dry, and then sand it down. One drawback of this approach with something as textured as wenge is that the clay gets into the natural figuring in the wood. It does sand out eventually, but it’d be nice not to have to do that. So as an experiment I tried putting down masking take before putting the clay in:
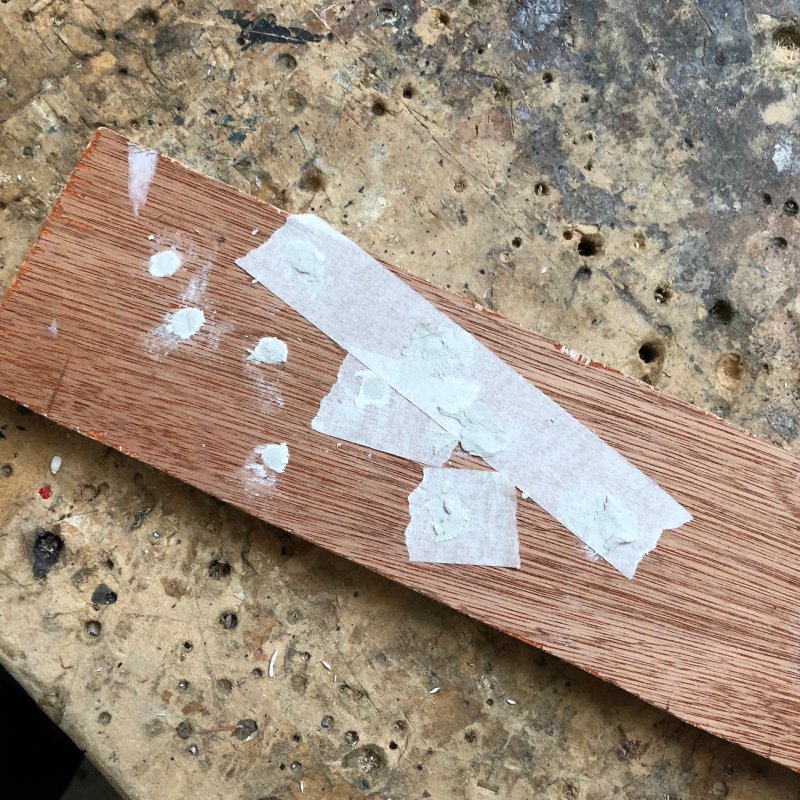
This worked quite well, although you do need to be careful that there is a nice clean edge around the hole with no frayed edges on the masking tape, as otherwise when you remove the tape later there isn’t a perfect join between the wood and they clay.
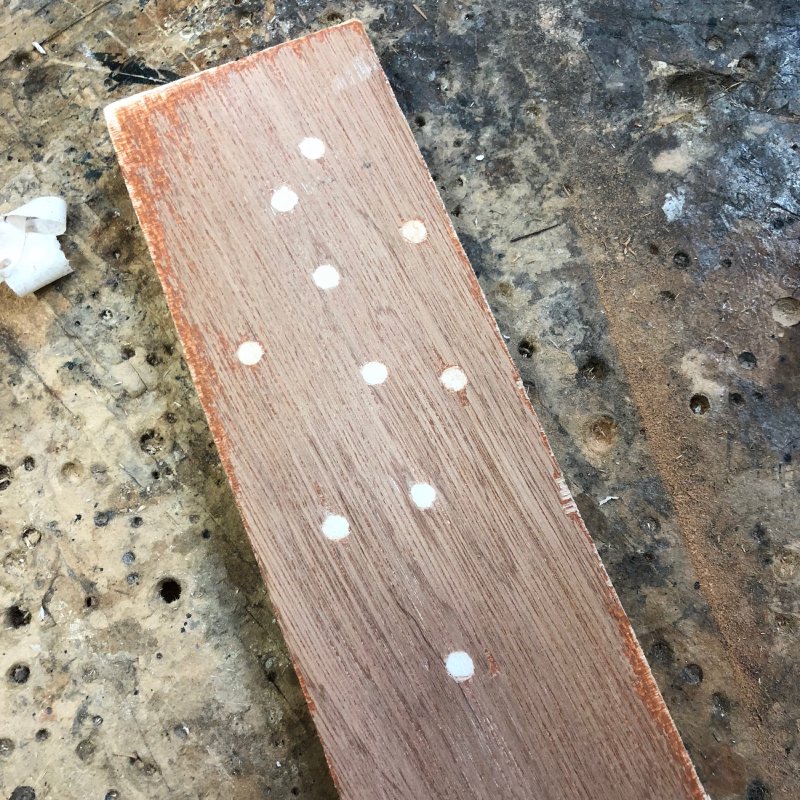
The only thing I’m on the fence about is whether I’m happy with the final finish on the clay. I like clay because it is a traditional finish - it’s now Fender used to make the dots on the guitars originally, and I prefer it’s natural finish to plastic “pearl” inlays. The one downside though is that as you sand the fretboard it will take on some amount of wood dust, which even with a light wood is visible. Here’s a close up of the last neck I made on the prototype offset:
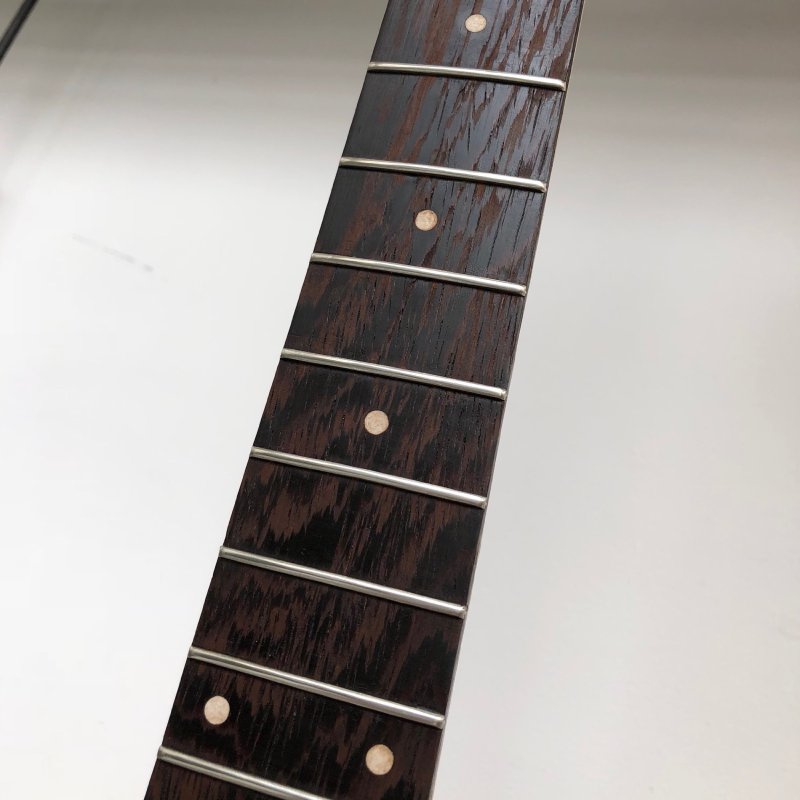
It’s not quite the quality I want when examined up close, though as a whole it’s not that noticeable, and it does give it a more natural finish, which is the aesthetic in general I want to go for.
On the neck that was already in progress I did do the fret insertion, which went smoothly.
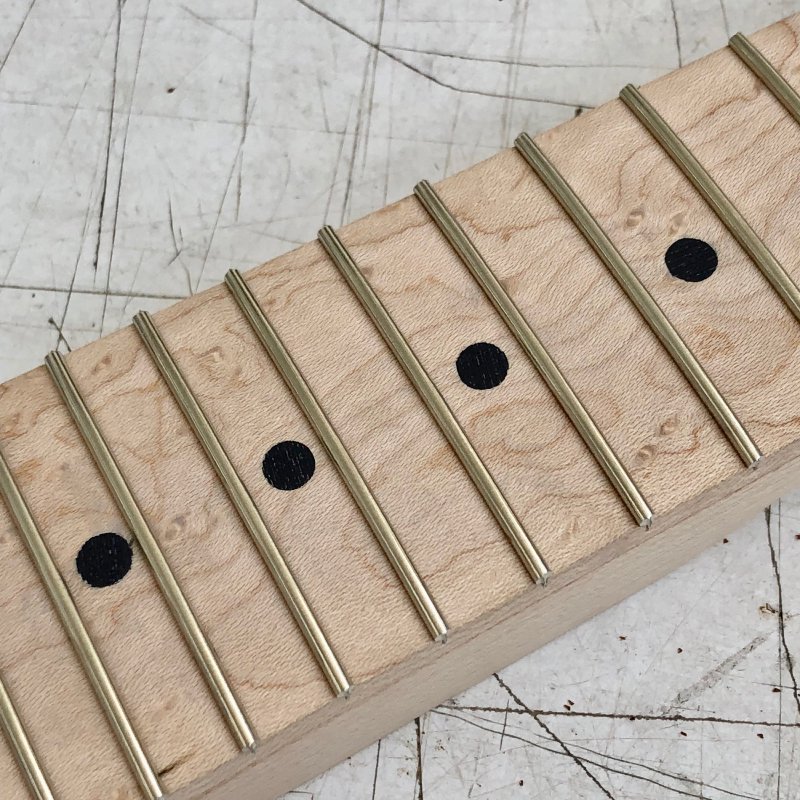
Certainly the more I do things like this the better I get; it is simply grinding like in WoW :) And this is in part why I’ve persisting in the finishing off of this recovery guitar made from bits that were damaged: it just gives me another chance to practice bits like fretwork to help me get slowly better. This neck is now taped up and ready for fret levelling, rounding, etc.
I’ve recently been trying to record a few videos of my guitars (and other lesser known brands, like Fender) through my amp, and I realised that the sound quality recording through my phone is good enough for a “what is he playing” but really doesn’t pick up the tone that I’m nearing in the room very well. So I decided it was finally time to get a proper microphone for such videos.
After much research I ended up ordering a Sennheiser e609 microphone, which is a dedicated amp microphone, and has a low profile so won’t get in the way and be something I trip over all the time. I then needed something to let me plug the microphone into my phone, and for that I’ve ordered a ZOOM U22 interface, which will take both an XLR microphone or a guitar direct in (assuming I’ve understood the manual), and has a USB out that is compatible with the iPhone USB converter dongle, or can be plugged into my laptop.
It’ll be a week or so before they turn up, but I’m looking forward to trying to capture some better tonal examples of my guitars and amp in action.
The spindle sander I ordered last week turned up, and I’ve installed it at Makespace. Many thanks to Matt for the recommendation.
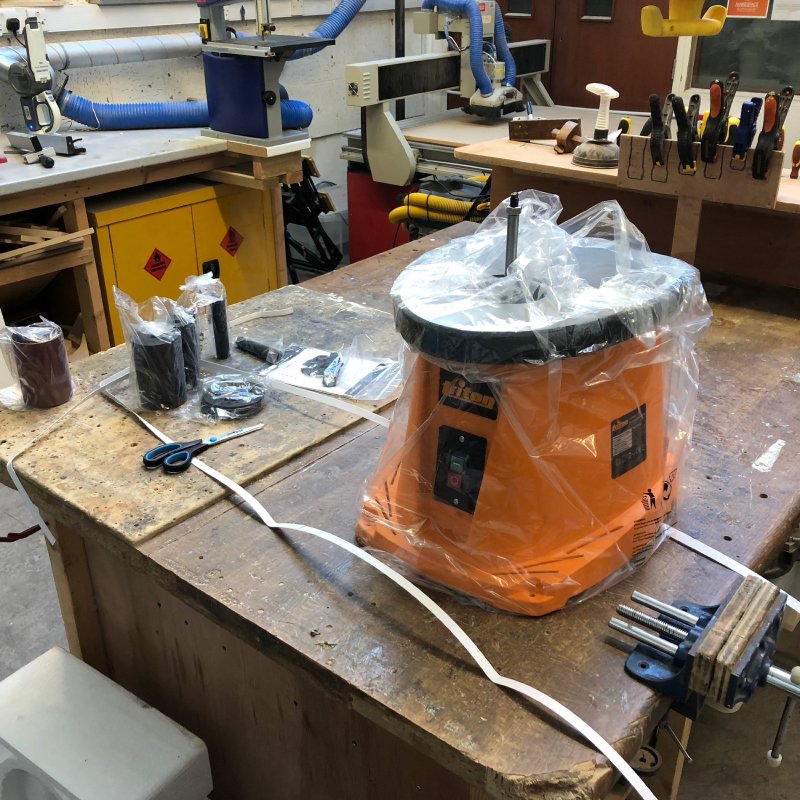
I’m actually quite impressed with the finish this thing gets with the stock 80 grit inserts, much more smooth than I’d expected, which I guess is down to the oscillating motion the spindle does whilst sanding, but whatever the reason the results are great, and it’s going to make sanding guitar bodies so much easier.
At the weekend I went to the Festival of Maintenance, a one day event in London celebrating the people who do maintenance as opposed to create new things, and a look at the issues they face.
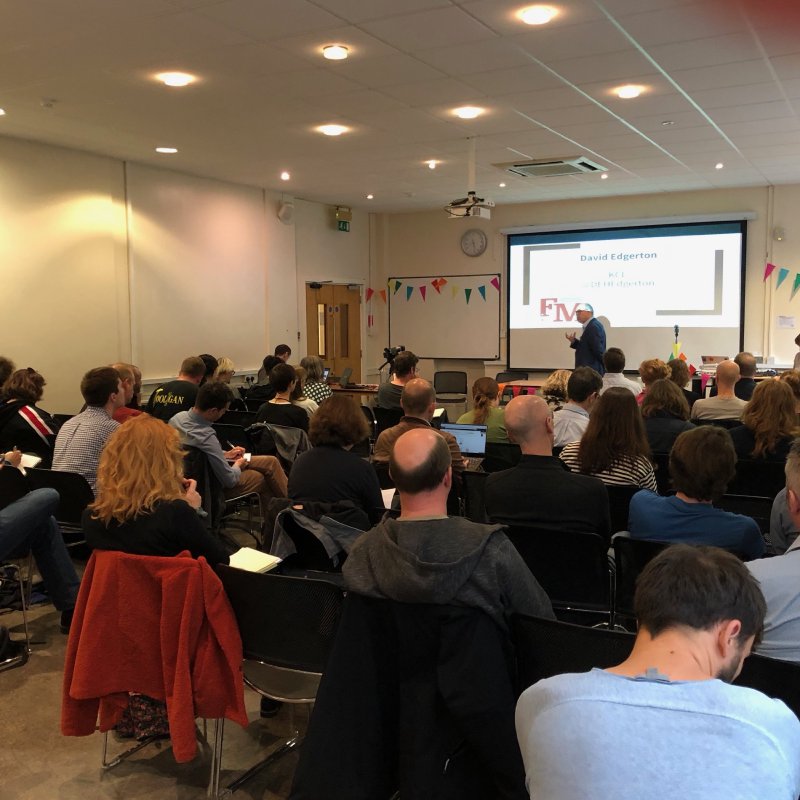
The talks covered a wide range of domains, from social housing, to documenting the HTML standards, to gorilla maintenance of your local area when no one else will. It was a very good day, with lots to think about.
I did remind me that I’ve been meaning for a while to push the fact that I’m happy to repair and setup of existing guitars, and that’s something I need to update this website for to make it more prominent. Both it’s a good thing to do environmentally in terms of keeping existing instruments in circulation, but also when I do guitar repair work it’s very educational seeing how other guitar manufacturers have approached things (something that Juha Lottenen was advocating also when I visited him).