A week in the shop and in a field
Published 6 Aug 2018
Last week I cut the neck for guitar #5, the much delayed first commission custom build, and this week I cut the body. As stated last week, I still don’t trust the CNC Router at Makespace particularly, but between the desire to make some progress and my now better understanding of the machine itself, I felt time had come to re-roll the dice. I was more nervous with the body compared to the neck for two reasons: firstly, although the wood from which the neck is cut is more expensive in monetary terms, a body blank represents half a day to a day of work by time I get to this point, so is more expensive to me personally; secondly, the body requires more cuts and more complex cuts than the neck, so more opportunity for the CNC Router to get confused and do the wrong thing.
However, like the proverbial kettle that never boils, it seems that by watching the CNC router like a hawk for the entire process (my thumb hovering over the abort button at all times), I was able to stave off failure, and the body came out all okay.
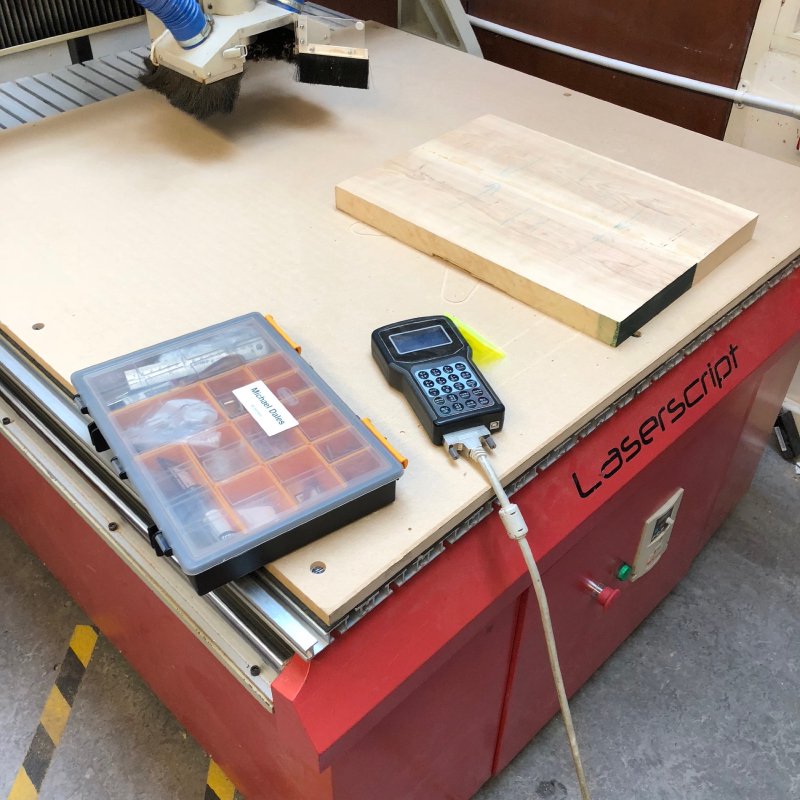
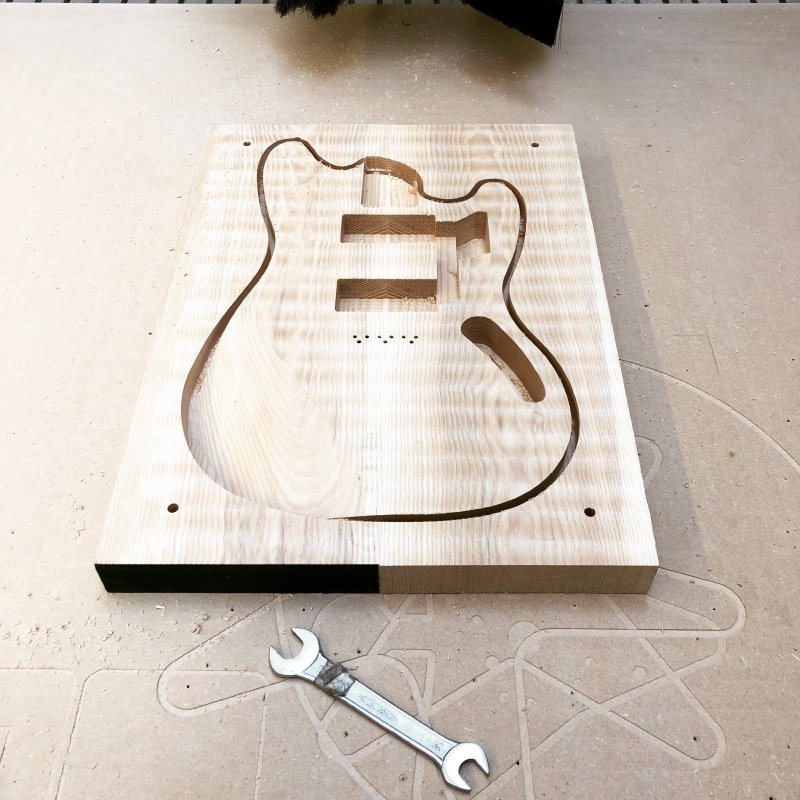
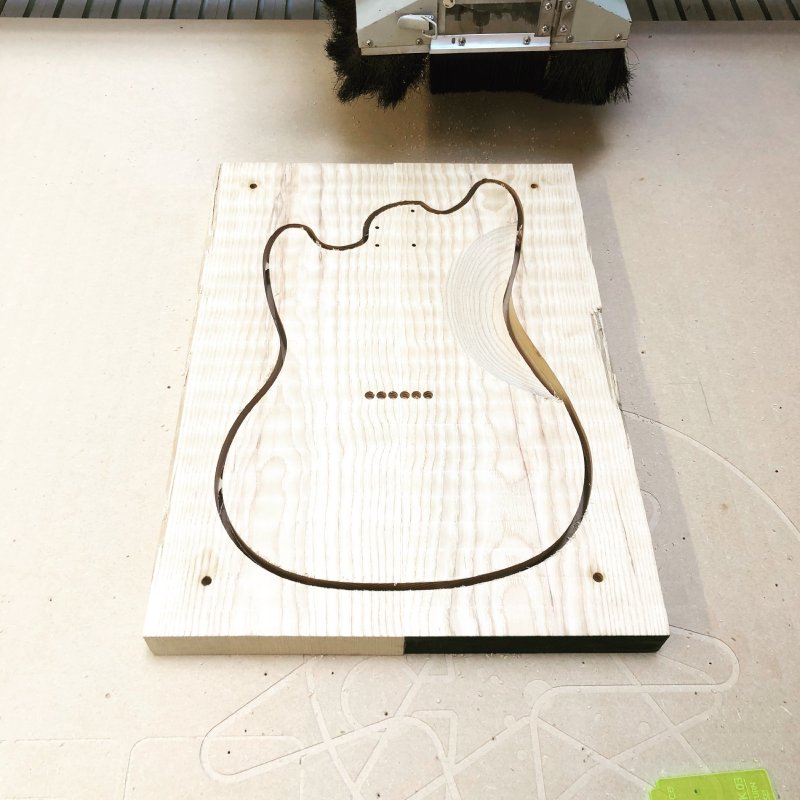
There’s much relief on my behalf that this is done. Now all I need to do is make the fretboard and we’re on route to getting this guitar onto the hand making part.
A couple of learnings from making the body. Firstly, I utilised the discovery I documented in last week’s notes that the machine’s ability to find the origin after it’s been powered off and on is more accurate than people suspected, to within a tenth of a millimetre. This meant I was able to make the guitar body over two days due to being short of time, rather than having to do it all in one session (CNC routing a body like this can easily take 4 or 5 hours all in). As the saying goes, the proof is in the pudding, and after I finished machining the body the seam where it was cut from the front side on day one and the rear side on day two is very close: as closed as I’d expect had I flipped it anyway, so I’m very happy there.
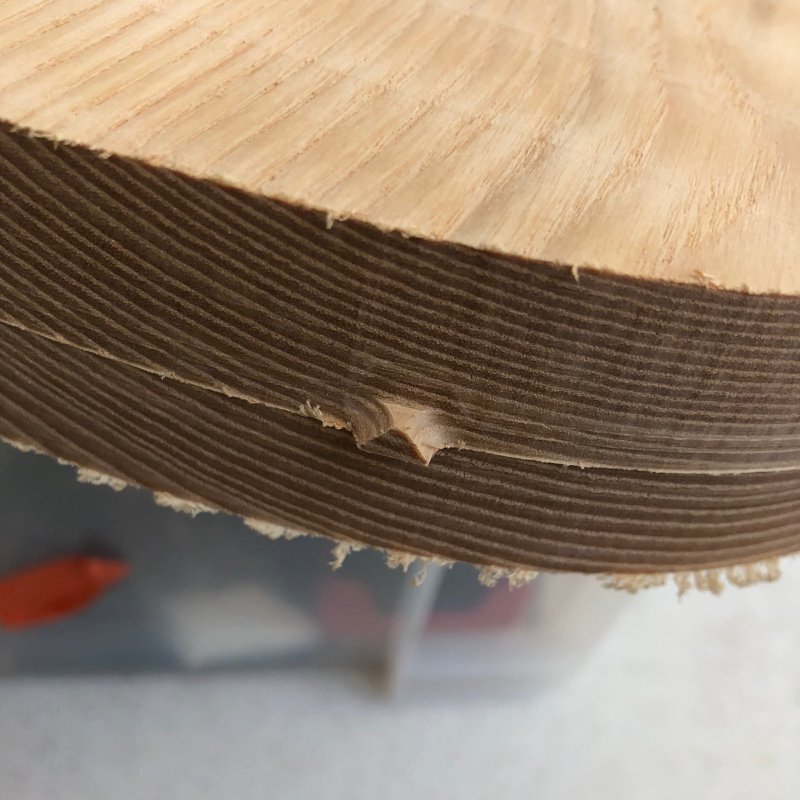
The other learning is in the triangular tab shape there. Most design tools insert rectangular tabs to hold pieces being cut out in place, but the down side of rectangular tabs is that the tool is briefly paused in the X/Y plane whilst it moves up and then later down, and at this point it will wobble slightly, leaving a groove that has to be sanded out. I spotted Fusion 360 has an option to make triangular tabs, which mean that the tool never has to dwell in one position, and so there’s no ghost grooves around this tab.
Next up for this body and neck now will be sanding. I finally gave in trying to sand by hand, and upon the advice of Matt I’ve got myself a proper orbital sander along with some professional quality sanding disks, so hopefully making the body nice and polished will be a lot easier.
This was about the only progress I made in the shop, as I spent the later half of the week watching live music for a change over at Wilderness Festival down in Oxfordshire. In the past there’s not been a wealth of music that has been of the style I’d normally go for (though there’s been good stuff that I’ve discovered that way), but this year they had a new stage, called the Hereafter stage, which was programmed with lots of great blues rock bands.
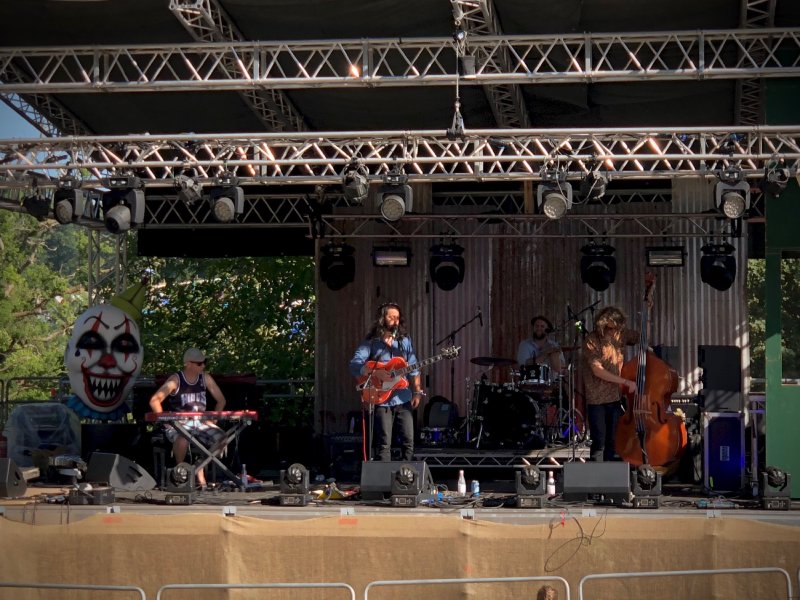
I’ll write up a list of my faves here shortly once I’ve caught up from being in a field without Internet for 4 days.