A week in the shop
Published 8 Oct 2018
This week has mostly just been a week of graft, getting the two necks moved along: the maple on maple one for the recovery offset build (or painters tape on maple as it has looked most of the week), and the wenge on birds-eye maple for the commissioned offset build.
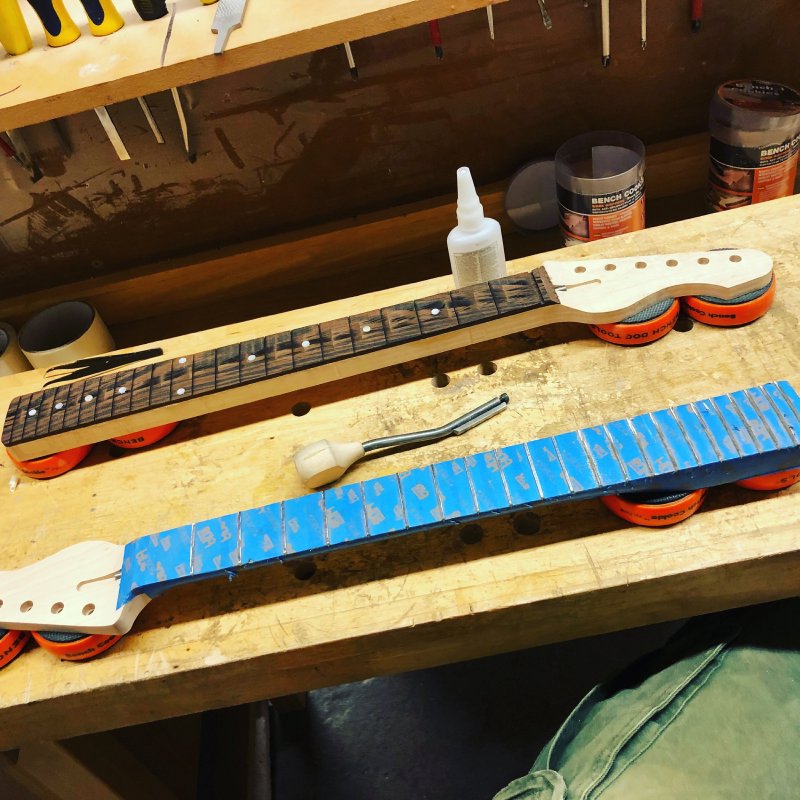
The recovery offset neck is slightly ahead of the commission offset neck, deliberately so given it’s been a few months since I did the fiddly bits of making a neck and I might as well get practice on the less pressured build first. On the recovery neck I just did the first pass of the fret work all the way through to, but not including, the polishing off the frets. They’re all level now, and the ends just need a little tweaking before I do the polishing, but overall this one is looking good.
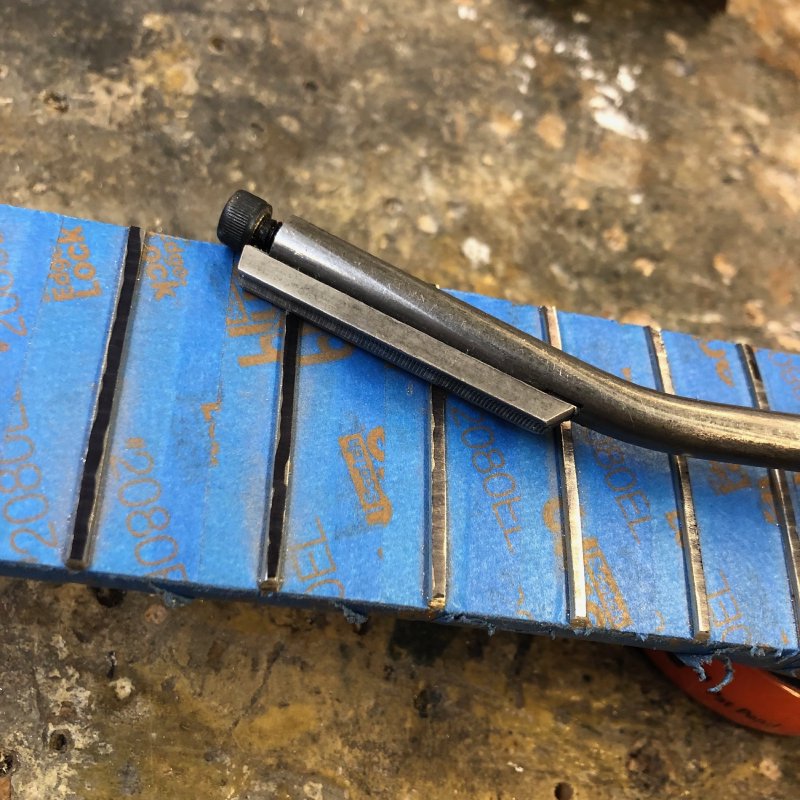
I wrote a few weeks ago about how I wasn’t happy with the finish of using clay inlays, and so I decided at the last minute to just go for pearl effect inlay dots on the commission neck. However, I had to do a sort of hybrid of both, as I’d drilled the dot holes on the assumption I would be using clay inlays, which require more depth, so they were a mm or so deeper than I needed to glue in the pearl plastic inlays (3mm deep vs the 2mm deep inlays). So to get that mm back I used a little clay and made the worlds smallest coffee tamper using a spare inlay dot and a cocktail stick to let me press the clay down properly :)
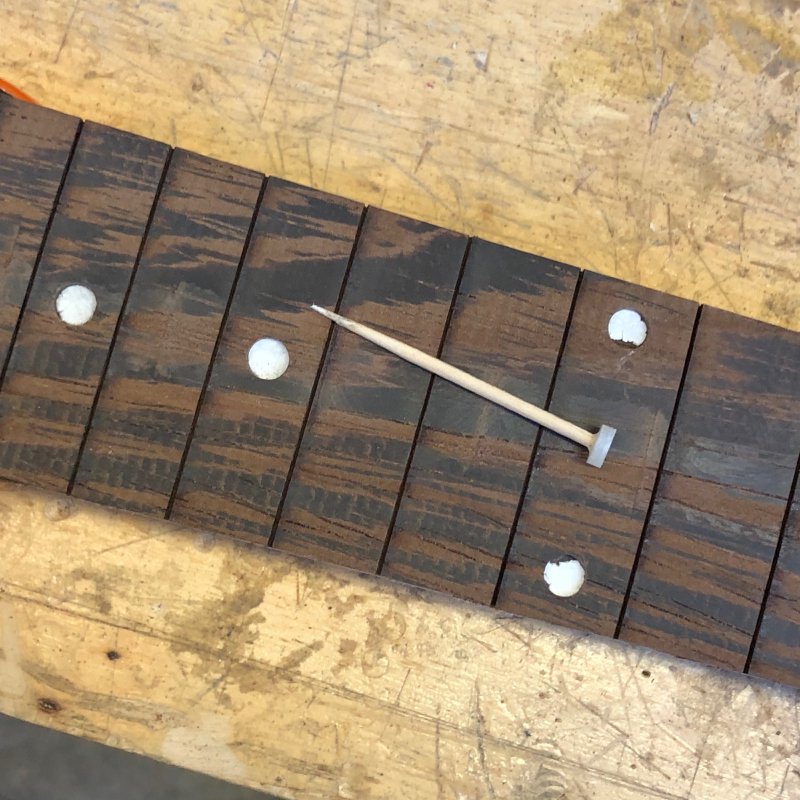
I let the clay set for a day and then glued in the pearl inlay dots and they sat perfectly That done I’ve then been sanding the radius in and making sure the fret slots are kept clean. The wenge has needed much more sanding to get the machine marks out than the maple did: I think the more brittle darker bits of wenge took more marks than the maple did, so that’s a learning for next time I machine a fretboard blank. But now it’s radiused and ready for fretting in the next week.
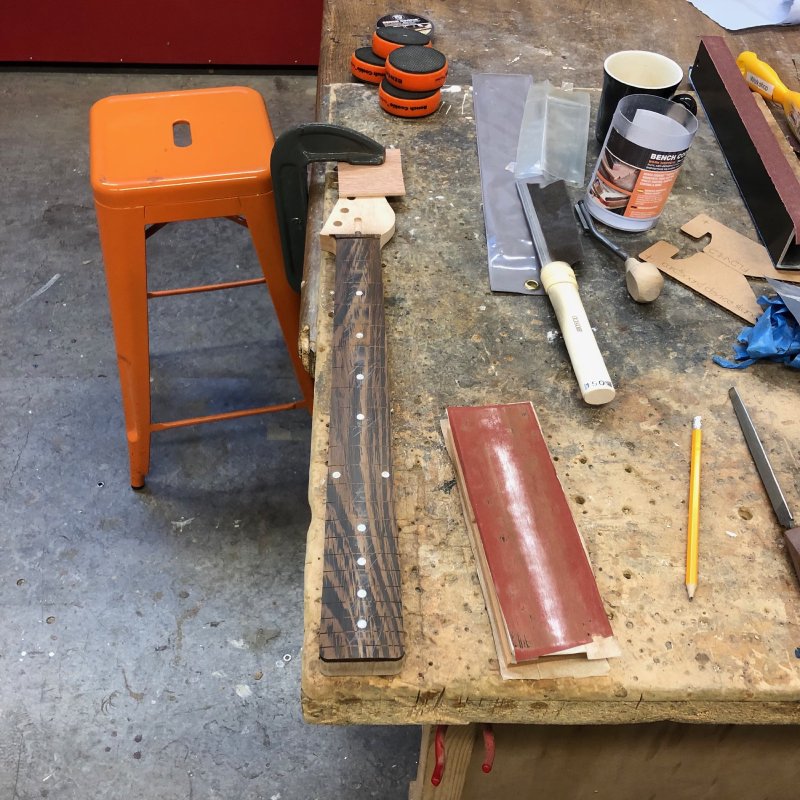
The top of the hill is almost insight for these: after fretwork it’s finishes and electronics, none of which are quite so much stress and graft as fretwork.
t’s nice to find oneself in a little community, even if I’m a total amateur compared to the other two luthiers I know in Cambridge. My friend Matt has a spray booth now, and so I’m going to have a go at spraying the recovery offset’s body in the near future. Normally I’d stain and oil the body, but given the repair I had to make on the recovery body is visible on the surface, but totally smooth to touch, I figured this was a good time to try out painting. I have been asked in the past to do painted guitars and have said no, so it’s a useful learning step to enable me to say yes to that in the future. I have some prep work to do, notably using grain filler which I’d not normally bother with, so that’s on my todo list for the next couple of weeks.
Jamie, who builds acoustics, got in touch asking if there was anything at Makespace where we might make some 0.5 mm holes, to help with a build he has on at the moment, and so I can do my bit to help for a change, and this coming week I’ve arrange with Jamie that we’ll see if we can use the laser cutters to solve his problem.